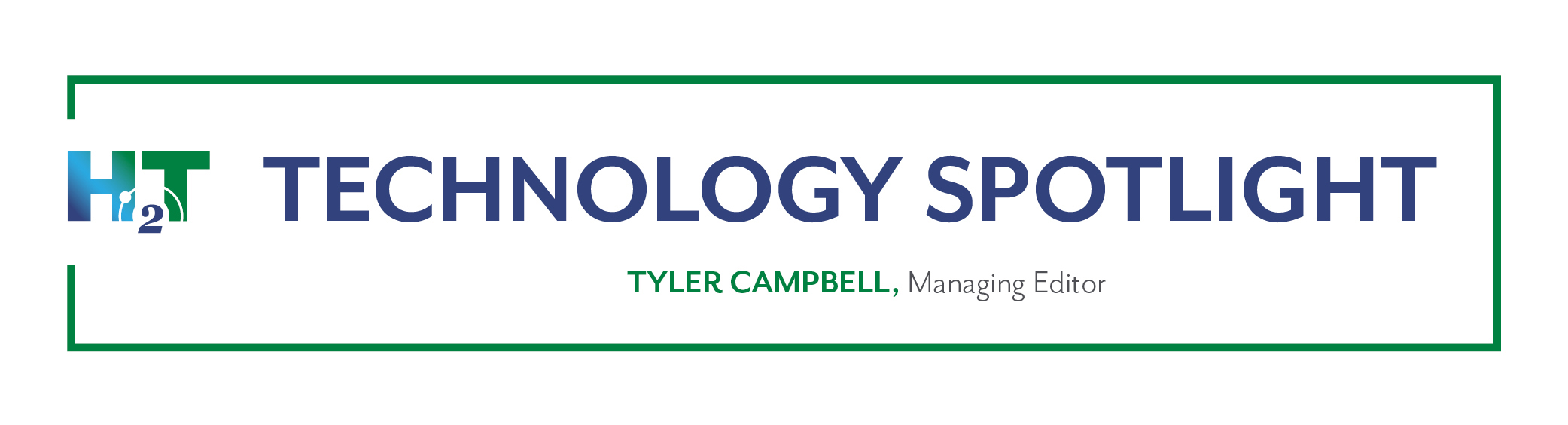
H2 EQUIPMENT
Baker Hughes launches new H2 pressure
sensor technology
Baker Hughes has launched its latest Druck H2-rated
pressure sensors. Designed to offer longer-term stability and withstand harsh
environments, the hydrogen (H2) pressure sensors can be used in
various applications, including gas turbines, H2 production
electrolysis and H2 filling stations.
Long-term exposure to H2 gas degrades the
performance of a pressure sensor, specifically through H2 permeation
and embrittlement of the isolation diaphragm, meaning the construction of a H2
sensor is key to maintaining accuracy and stability. Baker Hughes’ latest Druck
H2 pressure sensors apply high-performance barrier coating
technology to protect the sensor element from the harsh effects of H2,
providing customers with a market-leading minimum lifespan of 5 yr across a
wide range of pressures.
Teledyne Gas & Flame Detection releases an enhanced
version of the GS700-Hydrogen
Whether operating with natural gas, pure H2 or H2
blends, the portable GS700-Hydrogen simplifies gas detection across
outdoor and indoor leak detection, purging, barholing and pipeline gas testing
applications. The fully ATEX-certified instrument enables utilities to
determine the source of gas leaks quickly.
The development of the lightweight (1.4 kg) yet durable
GS700-Hydrogen was supported by comprehensive field trials aligned with the H2
transition efforts of prominent UK utility companies SGN and Northern Gas
Networks. In Scotland, SGN’s H100 Fife project will establish a green H2
gas network in Levenmouth, Fife.
This pipeline, entirely dedicated to 100% H2,
will run parallel to the existing natural gas distribution pipeline, providing
customers with a choice between the two gases. SGN collaborated with Teledyne
Gas Measurement Instruments, a Teledyne GFD brand, to develop the
GS700-Hydrogen. This collaborative process ensured the instrument’s suitability
for emergency response and engineering teams, enabling them to precisely detect
and locate H2 and natural gas leaks. The collaboration resulted in refining
the instrument's operation and validating its technology.
Teledyne GMI subsequently partnered with Northern Gas
Networks for the UK’s H21 H2 homes project. Northern Gas Networks
adopted the GS700-Hydrogen to ensure safety within its H21 networks and
measure H2 during activities like purging and pipeline commissioning.
PLIDCO launches new line of H2-compatible
fittings
PLIDCO has introduced a new range of products for H2
pipelines in response to the emerging transition toward H2 and other
alternative energy sources. PLIDCO’s products are ideal for H2, oil,
gas, water, chemical, steam, slurry and other piping systems. The company’s high-pressure
fittings are designed and manufactured to meet the highest quality standards,
following the American Society of Mechanical Engineers (ASME) and American
National Standards Institute (ANSI) codes.
PLIDCO maintains an inventory of fittings compatible with H2
pipelines, allowing customers to stop leaks without shutdown or welding
in onshore and subsea environments. Each of its H2-approved products
meets U.S. quality standards and has distinctive green markings to
differentiate them, helping to ensure mistake-proof repairs.
Bosch releases gas spectrometer to analyze H2
The Bosch optical gas spectrometer (OGS) is an advanced gas
analysis system that provides real-time, on-line and in-line gas composition
and concentration monitoring. However, its applications are not limited to H2
and natural gas mixtures. The OGS can analyze diverse gas mixtures for their
molecular constituents. With the OGS, users can achieve precise control over
gas mixtures and processes, improve operational efficiency and reduce gas
emissions in various applications. The OGS revolutionizes Raman spectroscopy
and will be available in the European market from Q2 2024.
H2 PRODUCTION
H2U completes performance and durability tests for
non-iridium catalysts
H2U Technologies has performed durability tests on new,
lower-cost, iridium-free catalyst materials that demonstrate a projected
lifetime of 25,000 hr. This durability milestone represents a significant
breakthrough and addresses supply chain bottlenecks for sustainable H2
production with proton exchange membrane (PEM) electrolyzers.
Discovering non-iridium catalysts for commercial
applications has been challenging, as novel materials often degrade rapidly
under the harsh acidic conditions of the oxygen evolution reaction (OER). For
perspective, the best iridium-free catalysts known to date offer lifetimes of
approximately 1,000 hr—1,400 hr. With a baseline of > 4,000 hr of continuous
operation thus far, H2U's iridium-free catalysts, tested at 10x higher current
density, demonstrate projected lifetimes of > 25,000 hr. H2U catalysts are projected
to last at least 6 yr for targeted applications, such as in PEM electrolyzers
paired with curtailed renewables.
As the H2 economy grows and the demand for H2
increases, maintaining catalyst performance without relying on iridium becomes
even more critical. Durable catalysts enable the scalability of H2
production and utilization technologies by reducing the frequency of
replacements and associated costs. The reliance on iridium has raised industry
concerns, as the U.S. Department of Energy has recently categorized iridium as
the sole material in the H2 sector at high risk of supply
disruptions.
H2U's innovative catalysts are cost-effective and more
readily available than iridium. Utilizing these affordable alternatives expands
the possibilities for electrolyzer stack design, enabling H2U to explore
avenues unrestricted by ultra-thin catalyst layers and low usage of catalysts.
This flexibility significantly reduces capital expenses, producing more
affordable delivered H2.
Technip Energies adds Casale’s ATR technology to deliver
large-capacity H2 solutions
Technip Energies has added advanced autothermal reforming
(ATR) technology to Blue H2 by T.EN™, its fully-integrated,
low-carbon H2 solutions. It is part of Capture.Now, Technip
Energies’ strategic platform for carbon capture, utilization and sequestration
(CCUS) delivers technology and solutions from a single provider tailored to
meet clients’ specific decarbonization and performance needs.
Blue H2 by Technip Energies (T.EN) is a suite of
fully integrated, cost-efficient and low-carbon H2 solutions. As a
global leader in H2, Technip Energies has recently added oxidative
reforming-based technologies in partnership with Casale to its extensive range
of proprietary steam methane reforming (SMR) technology solutions.
Casale’s ATR, combined with Technip’s parallel reformer and
carbon capture, is a cost-effective way to produce low-carbon H2 at a
large scale with optimized steam production. ATR breaks the upper capacity
limit of traditional H2 plants, which were economically constrained
by the size of the SMR, and enables large-capacity, ultra-blue H2
production with up to a 99% carbon capture rate.
Tailored to meet clients’ specific decarbonization and
performance needs, Blue H2 by T.EN comprises the proven building
blocks required to create optimal low-carbon H2 solutions and
deliver them with increased performance and project certainty. This results in
the best possible levelized cost for blue H2 with the lowest carbon
footprint regardless of plant feedstock, reforming type or plant capacity.
Rice University researchers discover method to harvest H2 from
plastic waste
H2 is viewed as a promising alternative to fossil
fuel, but the methods used to produce it either generate too much carbon
dioxide (CO2) or are too expensive. Rice University researchers have
found a way to harvest H2 from plastic waste using a low-emissions
method that could more than pay for itself.
Green H2—produced using renewable energy sources to split
water into its two component elements—costs roughly $5 for just over 2 lb. Though cheaper, most of
the nearly 100 MMt of H2 used globally in 2022 was derived from
fossil fuels, generating roughly 12 t of CO2 per t of H2.
The researchers exposed plastic waste samples to rapid flash
Joule heating for about 4 sec, increasing its temperature to 3,100°K. The
process vaporizes the H2 present in plastics, leaving behind
graphene—an
extremely light, durable material made of a single layer of carbon atoms.
HPQ Silicon files patent for autonomous, low-carbon
pressurized H2 production system
HPQ Silicon has announced its Lyon-based, affiliated
company, Novacium, has filed a patent application for a low-carbon footprint,
chemical-based, on-demand and high-pressure autonomous H2 production
system.
The new H2 production system uses a chemical
process to liberate H2 from specific low-cost, low-carbon footprint
and non-hazardous alloys. Furthermore, the H2 produced by the
chemical process directly reaches industry-standard pressure levels, typically
ranging from 200 bar–1,000 bar.
Unlike traditional electrolysis-based H2
production systems, Novacium's process operates without electricity, extensive
storage and complex transportation infrastructure, offering a truly autonomous
solution.
The dual-application process, designed for military and
civilian uses, addresses a potential client's need for a low-carbon footprint,
on-demand, high-pressure autonomous H2 production system deployable
anywhere globally, even under off-grid conditions, with safety as a top
priority.
Novacium is engaged in discussions to secure grant financing
from two potential clients to cover 35%–75% of the costs to deliver the first
working prototype of the system by the end of 2024.
Ionomr Innovations validates stability and performance of
its anion exchange membrane (AEM) electrolyzer
Ionomr Innovations has completed the Shell GameChanger
Accelerator powered by the National Renewable Energy Laboratory (NREL), which
provides promising cleantech startups with access to financial resources,
state-of-the-art facilities and world-class technical experts. Ionomr has
created and is commercializing a new generation of high-performing,
environmentally friendly electrochemical materials that are essential building
blocks of a green H2 economy.
Working with experts at NREL and Shell and applying
industrial and energy agency models, Ionomr has further validated its Aemion+
AEM, providing performance and lifetimes capable of reducing the lifecycle
system capital cost of H2 production equipment by water electrolysis
by more than 40%. Aemion+ was shown to increase the output of iridium-free
electrolysis systems for water electrolysis while repeatedly demonstrating
stability from more than 800 hr of tests. It also demonstrated various
efficient and stable configurations for directly converting captured CO2 into
liquid fuels, improving output three-fold.
Ionomr’s Aemion+ polymers and membranes reduce the cost of
green energy because they are designed to eliminate the expensive and scarce
components conventionally used for water electrolysis. Materials such as
iridium and titanium are replaced with less expensive materials, while
performance is enhanced over traditional low-cost alkaline systems and readily
pairable with intermittent renewables due to its high ramp rate capability. The
membrane technology creates an ultra-stable, lower-cost, safer and more flexible
system.
Ionomr’s membranes and polymers are synthesized from an
environmentally friendly hydrocarbon base, using a fraction of the energy in
their production. They demonstrate no bioaccumulative tendencies and are
non-toxic to the environment through production, use and end-of-life. They
present the ideal replacements for conventional membrane and polymer products,
all containing per- and poly-fluoroalkyl substances.
DuPont introduces ion exchange resin for green H2 production
DuPont has launched its first product dedicated to green H2
production—the
DuPont™ AmberLite™ P2X110 Ion Exchange Resin. This newly available ion exchange
resin is designed for the unique chemistry of electrolyzer loops to support H2
production.
H2 can be produced by several methods from
different feedstocks. Green H2 can play several major roles in the
energy transformation, contributing to the decarbonization of transportation,
heat and energy, and as greener feedstock. Electrolysis is the process of
electrically splitting water molecules
into H2 and oxygen gas, and while there are various types of
electrolyzers, they all rely on high-purity water as the feedstock to produce H2.
Designed to endure the thermal and chemical challenges
presented in an electrolyzer, the AmberLite P2X110 Ion Exchange Resin's recipe
offers durable and reliable water quality that helps prevent contaminant
build-up in the electrolyzer loop. These customized features and improved
removal capacity present a differentiated option for electrolyzers with more
service time than industry generic resins.
H2 STORAGE AND TRANSPORTATION APPLICATIONS
DNV awards approval in principle (AiP) to HD KSOE’s H2 system
for liquefied H2 carrier
DNV has awarded an AiP to HD Korea Shipbuilding &
Offshore Engineering (HD KSOE) and its subsidiaries HD Hyundai Heavy Industry
(HD HHI) and Hyundai Mipo Dockyard (HMD) for their new H2 system. HD
KSOE aims to complete the development of the H2 carrier technology
that enables large-capacity H2 transportation and storage by around
2030.
Sustainably produced zero- and low-carbon H2 has
been identified as a key part of the world’s energy transition. Efficient
transport by ship faces several challenges, including the complexity of holding
H2 at –253°C, some 100°C colder than LNG, at large scale. Finding
solutions to this challenge is vital, as shipping has an important role in
unlocking the use of H2 in decarbonizing heavy industries (e.g.,
steel and cement production).
HD KSOE's new system utilizes boil-off gas from H2
transport for a hybrid propulsion system, integrating H2 engines and
fuel cells. HD KSOE and partners like Woodside Energy and Linde Engineering are
exploring new H2 transportation and storage solutions, aiming to
commercialize their advancements by 2030. H2T
Transforming the U.S. into a widespread H2 hub
In October 2023, the Biden-Harris Administration and the U.S. Department of Energy (DOE) announced $7 B in investments to launch seven nationwide Regional Clean Hydrogen Hubs (H2Hubs) throughout the country. This is part of President Biden’s Investing in America agenda, an attempt to reinvigorate the U.S. economy by bringing manufacturing back to America and prioritizing the commercial deployment of low-cost, clean hydrogen (H2). The H2Hubs are projected to produce approximately 3 MM metric tpy of H2, significantly contributing to the U.S.’s 2030 H2 production and carbon dioxide (CO2) reduction targets (FIG. 1). According to the DOE, the hubs were selected depending on five main factors:
The seven H2Hubs will be scattered across different U.S. regions, including the Pacific Northwest, California, the Gulf Coast, Heartland, Midwest, Appalachian and Mid-Atlantic regions (FIG. 2). The Pacific Northwest H2 hub (PNW H2) will be located across Washington, Oregon and Montana, solely utilizing renewable energy to produce green H2 through electrolysis and potentially reducing CO2 emissions by 1 MM metric tpy.
The prime contractor is the Pacific Northwest Hydrogen Association, which includes Air Liquide Hydrogen Energy US LLC, Amazon.com Inc., ALA Renewable Energy LLC, Atlas Agro, Centralia College, Mitsubishi Power Americas Inc., Northwest Seaport Alliance NovoHydrogen Development Inc., PACCAR Inc., Portland General Electric Co. (PGE), Puget Sound Energy (PSE), PUD No. 1 of Douglas County, St. Regis Solar LLC, Synchronous LLC dba First Mode, Twin Transit, USA Fortescue Future Industries Inc. and Williams Field Services Group LLC, and the federal cost share is up to $1 B.
The California H2 hub will span the state, producing H2 from renewables and biomass, eventually aiming to pave the way to decarbonizing heavy-duty transportation and converting ports to export H2. Furthermore, the hub aims to cut CO2 emissions by 2 MM metric tpy. The prime contractor for the project is the Alliance for Renewable Clean Hydrogen Energy Systems (ARCHES), a statewide public-private partnership designed to accelerate renewable H2’s contribution to decarbonizing California’s economy, and the federal cost share is up to $1.2 B.
The Gulf Coast H2 hub will be spread across the Texas coast, producing H2 via natural gas coupled with carbon capture and electrolysis. This hub will also integrate salt caverns to store H2 and H2 pipelines for transport. The Gulf Coast H2 hub is projected to reduce CO2 emissions by approximately 7 MM metric tpy. The prime contractor for this hub is HyVelocity, an industry-led H2 hub that includes seven core industry partners: AES Corp., Air Liquide, Chevron, ExxonMobil, Mitsubishi Power Americas, Ørsted and Sempra Infrastructure. The federal cost share is up to $1.2 B.
The Heartland H2 hub will be located across Minnesota, North Dakota and South Dakota to produce clean fertilizers, such as ammonia, and reduce green H2 production costs. Furthermore, the region will explore utilizing H2 for power generation. The Heartland H2 hub is projected to reduce CO2 emissions by 1 MM metric tpy. The prime contractor for this project is the Energy and Environmental Research Center (EERC), and the federal cost share is up to $925 MM.
The Midwest H2 hub will be in Illinois, Indiana and Michigan, decarbonizing sectors such as steel and gas production, power generation and aviation, utilizing renewables, natural gas and nuclear energy. The hub aims to reduce CO2 emissions by 3.9 MM metric tpy. The prime contractor for this hub is MachH2, and the federal cost share is up to $1 B. Notable partners in this alliance include Air Liquide, ArcelorMittal, Argonne National Laboratory, Bloom Energy, bp, Charbone Hydrogen, ExxonMobil, Gevo, Nalco Water, Plug Power and Rockwell Automation.
The Appalachian H2 hub will be in West Virginia, Ohio and Pennsylvania, and plans to leverage natural gas coupled with carbon capture to produce blue H2. The hub aims to reduce CO2 emissions by 9 MM metric tpy. The prime contractor for this hub is Battelle, and the federal cost share is up to $925 MM.
The Mid-Atlantic H2 hub will be in Pennsylvania, Delaware and New Jersey, seeking to utilize renewables and nuclear electricity to decarbonize heavy-duty transportation, industrial process improvements and combined heat and power. The hub anticipates reducing CO2 emissions by 1 MM metric tpy. The prime contractor for this hub is the Mid-Atlantic Clean Hydrogen Hub (MACH2), and the federal cost share is up to $750 MM. Notable MACH2 partners include Air Liquide, Bloom Energy, Braskem, Dupont, Enbridge, Hilco and PBF Energy.
If successful, these H2 hubs have the potential to substantially ramp up clean H2 production in the U.S. Coupled with the government’s investments to advance H2 production technologies (e.g., electrolyzers), the $1/kg in a decade milestone set by the DOE may be in reach. H2T
H2Tech November 2023
H2-Tech.com