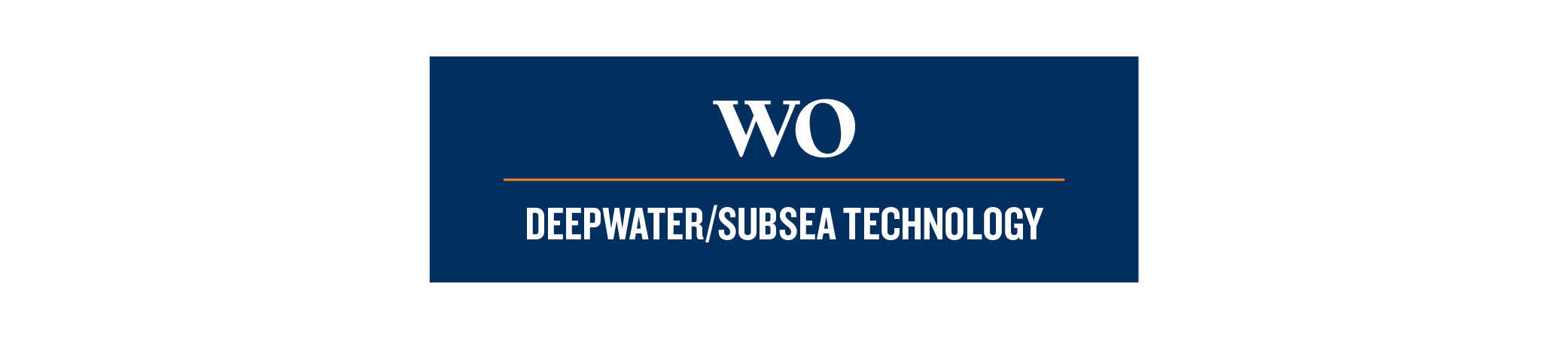
Reinventing the subsea production
system: The first 20,000-psi SPS
A new,
20,000-psi, subsea production system has been developed and is now being manufactured
and factory-tested for installation in the Gulf of Mexico. The system was rigorously
qualified by an independent third party to ensure all previous technology gaps
were addressed. This story explains the technology’s development.
Although an
onshore production system rated for 20,000 psi exists, the subsea version had
remained unrealized until a joint industry program was initiated in June 2015
between an operator in the Gulf of Mexico and OEM OneSubsea®, SLB’s subsea
technologies, production and processing systems business.
Now commercially
available, the 20,000-psi subsea production system (SPS) includes new technologies
required to meet the demands of high-pressure, high-temperature (HPHT)
conditions. Development included conducting rigorous qualification according to
API Technical Report 17TR8 guidelines for equipment used in HPHT environments,
which API defines as pressures greater than 15,000 psi or temperatures greater
than 350o F.
In
conjunction with HPHT qualification, an independent third-party (I3P) was
commissioned to perform an engineering review of the equipment design,
qualification and manufacturing plans, as required before the U.S. Bureau of
Safety and Environmental Enforcement (BSEE) can approve operator plans or
permits using the technology. The result of this extensive, comprehensive process,
shown in Fig. 1, is a safer, more sustainable approach for producing 20,000-psi
subsea fields.
Closing
technology gaps with teamwork. Extracting hydrocarbons from an offshore deepwater well with
shut-in pressures higher than 15,000 psi requires that every component of the
entire subsea system can handle these conditions across drilling, installation,
commissioning, production, intervention and transportation. This requirement has
revealed many technology gaps to be addressed in developing a 20,000-psi SPS.
To tackle
this broad challenge, a multidisciplinary global team was assembled. It was
decided to develop all the necessary technologies and equipment, as possible, within
the OEM’s organization to ensure that the development process and methods were
consistent and easy to monitor to keep their progress on schedule. The team’s HPHT
design strategy was to initially leverage existing lower-capacity designs by
reinforcing the geometry and using stronger materials. This was supplemented by
reducing overall loads by minimizing pressurized areas, pressure balancing and
offsetting weight, which also supported manufacturing sustainability. Considering
that the design team members were not necessarily located at the manufacturing and
fabrication plants, a “design anywhere, manufacture anywhere” approach was also
implemented, which was greatly facilitated by digitalization.
Highlights
of the new technology development and qualification required for the 20,000-psi
SPS are as follows:
Couplers.
Traditional use of
third-party technology for couplers was avoided through the development of
interchangeable wet-mateable electric and hydraulic couplers with debris
resistance. New robust seals also had to be developed, but overall, the number
of parts in the couplers was minimized to keep tolerance stack-up low. These
couplers enable more efficient footprint allocation, which allows fitting more
downhole lines in the subsea tubing hanger.
Gate
valves. Although
OneSubsea’s more than 60 years of OEM experience included a 20,000-psi-rated
gate valve for surface operations, the demands of the subsea environment
required new gate and actuator designs. The full suite of HPHT gate valves
developed for the 20,000-psi SPS includes 2-in. hydraulically-actuated and 5-in.
manually and hydraulically actuated valves for the tree system. The manifold
uses 5-in. hydraulically-actuated and 7-in. manual and hydraulic valves.
Connection
systems. Two subsea
tree-to-wellhead connector configurations were developed with the capacity to
withstand extensive pressure, bending and tension loading conditions while
efficiently interfacing with industry-recognized third-party lockdown profiles.
Four
ROV-operable vertical clamp connection systems with dual metal gaskets were
also developed with verified bending and torsional capacity at high pressures
for use on the tree system, jumper and flowline connections and choke insert.
Multiphase
flowmeter. Integrated
into the main production flow path of the vertical monobore subsea tree system,
the Vx Omni* subsea multiphase flowmeter enables HPHT subsea multiphase flow
testing, with a venturi throat design that can measure the flowrates of gas,
oil and water in any combination of proportions, from 0% to 100%. In addition
to the reliability provided by having no moving parts and fully redundant
electronics, 90% of the components are standardized, and their number is
reduced by two-thirds from prior-generation designs, Fig. 2.
Material
and welding qualification program. Years before verification against industry and regulatory
HPHT requirements was initiated, as part of the design process the
multidisciplinary team collaborated to collect foundational data. The qualified
materials include low-alloy steels (LAS) and nickel alloys, with nickel alloy
cladding over LAS also qualified for use with all production equipment for ASTM
Class HH steel. Additional testing was conducted for fastener documentation.
The results
of this testing program documented material performance within air, sour
production fluid, seawater and completion brine environments. From this basis,
the fatigue characteristics and equipment performance in various environments
were explored as an essential part of HPHT verification.
Integrated
multiphase pumping system and production manifold. Rated to 16,500 psi, this permanently-installed
large subsea structure houses a complete manifold section that connects up to four
wells and a boosting section that enables increased field production, with a
retrievable multiphase pump module, Fig. 3. This gravity-based structure
will be supported on one of the largest suction piles in the Gulf of Mexico.
Manufacturing
the necessary large, heavy-wall forgings, pipes and fittings required
developing and qualifying new manufacturing methods. The process valves for
operating the pump were similarly qualified for a 7 1/6-in. bore size, and they
incorporate a nonreturn valve and fail-open and fail-close hydraulic
spring-return gate valves.
Additional
new subsystems include a flow mixer to suppress slugs in the multiphase flow
and a pressure equalization circuit, for safer pressurization and
depressurization of the pump process section when using the pump control system
during intervention. At a system level, the new control logic approach reduces
the number of components by using the production tree subsea control module to
control manifold valves within the production manifolds and the integrated
manifold pump station.
Pump
module. Installed
with the integrated manifold pump station, the pump module is a retrievable
subsea structure featuring a helicoaxial multiphase pump with a maximum flow
capacity of 120,000 bopd, 2,320 psi of design differential pressure and a gas
volume fraction range from 0% to 100%, Fig. 4. The pump housing is
joined to the motor housing through a new flange,with a secure, dual-metal
gasket. Inside the housing is an electric motor with 4 MW of shaft power that
drives a multistage impelled pump joined by flexible coupling.
The pump’s dielectric
hydraulic fluid system lubricates the pump, cools the motor and acts as a
barrier to prevent process fluid from entering the motor by maintaining a
constant overpressure during all operation and intervention modes of the pump.
The fluid is supplied from a topside hydraulic power unit through the umbilical.
Mechanical valves ensure that the overpressure is maintained throughout rapid
increases or decreases of process pressure in the pump.
For flow
control, the pump uses a single-phase flowmeter on the discharge side.
Vertical
monobore tree. The
subsea tree was designed to house many of these newly developed technologies in
a compact package that ensures that the total weight and footprint are within
the capabilities of the system’s handling and testing facilities, Fig. 5.
Its other major innovation is the tubing hanger system, with lockdown and
orientation packages in a slim annular design, which, in combination with the small-footprint
couplers that were developed, allows space for 13 downhole lines.
Packaging
the 20,000-psi subsystems and demonstrating standards compliance. Project execution during the detailed
engineering phase had to meet several new challenges while staying on time and
on cost. An additional constraint was accounting for the added weight of the
components required for the vertical monobore tree system to control and direct
fluid flow at the elevated pressures.
The design
strategy to improve on lower-rated designs by increasing wall thickness and using
stronger, denser materials had the potential to add significant weight. But the
system still had to be transportable on water, land and air; conform to
offshore rig deployment and testing capacity; and dimensionally fit the maximum
height allowance and fatigue loads of cranes.
Our innovative
annulus routing path for shortening the tubing head spool by placing the primary
annulus valves horizontally aligned to each other, instead of the conventional
vertical arrangement, reduced both height and weight. Establishing
self-balancing layouts mitigated balance weight requirements, and the weight of
the thermal insulation on the pipework of the manifold structural frame was
optimized via thermal analysis studies.
It was
during this project phase that compliance to BSEE regulatory guidance, issued
as Notices to Lessees and Operators, was addressed. A team of the SPS subject
matter experts developed a foundational design philosophy toward globally
meeting HPHT design requirements, including previous alignment with API 17TR8, that
would eliminate numerous interpretation cycles. The coordination and
collaboration between all three entities was essential in establishing the
ground rules by which planning, execution and reviews involving the I3P,
operator and OEM would impact the schedule. The potential consequence of
missing just a single element within a guideline or standard could delay equipment
delivery by months, so maintaining this alignment has been critical to
maintaining timely progress.
The operator
also requested additional testing to reduce the risks associated with the first
deployment of equipment that has not been field-tested. Because it would be highly
inefficient to use the complete SPS assembly for testing parts, qualification
test fixtures with equivalent configurations, forces, friction properties,
debris introduction and other aspects were used.
Leveraging
digitalization for optimization and sustainability. In line with the industry’s trend
toward digitalization, emerging software solutions were employed to
significantly improve all aspects across every phase of the project. For
example, advanced finite element methods were used to analyze complex components
and assemblies. Admittedly, HPHT systems exert higher stresses and deflections
on structures, but traditional/conservative methods of analysis output
requirements for high-cost materials, with high yield strength and
unnecessarily thick cross-sections to support pressures. The software enabled
conducting realistic modeling of load cases without the need to build a
physical prototype.
Virtual
reality (VR) technology was used from the early stages of the project to
provide an immersive interactive experience with the production equipment and
simulate assembly operations and subsea operations, such as ROV interfacing. VR
also supported a live feed of the assembly, testing and manufacturing processes
to engineers and other subject matter experts for remote real-time witnessing.
This was especially useful in connecting with the I3P and operator when travel
restrictions were posed by the COVID-19 pandemic.
Having
digital tools for modeling and simulation also contributed to sustainability. This
approach accelerated the ability to affect weight reductions, as previously
mentioned, and shortened the prototype stage, both of which inherently reduced
embodied carbon emissions. Similarly, a new tooling system to reduce operator
installation time will help minimize carbon emissions from offshore facilities
and vessel usage during those operations.
Meeting
fabrication challenges with upgraded facilities and digital capabilities. The equipment-build phase included
upgrading the OEM manufacturing plants to state-of-the-art manufacturing and testing
facilities to address the size and complexity of equipment that was beyond
their previous 15,000-psi applications. The upgrade also included the testing
facilities. In particular, the test cells increased their pressure capacity,
footprint, and depth and added remote monitoring tools. New processes were
developed, such as using custom fastener preload equipment, ultrasonic
inspection methods and automated remote monitoring and testing capabilities for
the high-pressure test cells.
Virtual-build
simulation was incorporated in the manufacturing process to first assemble
products in a 3D virtual environment once the top-level assembly models and
procedure were released. This approach requires only a single engineer, not an
entire physical process and necessary materials and personnel, to confirm
sequence optimization, verify access to connections for validation, check for
incompatibility between assembly components and tooling, and confirm that all
areas for improvement are identified before starting the physical build.
All findings
are extensively documented and available across the design, manufacture,
assembly and test teams. The virtual build also helps in reducing HSE risks,
such as those posed by handling concerns. Following a “virtual first” process has
proactively mitigated sticking points in the physical process to reduce
downtime during subsequent assembly and in turn, reduce nonconformance issues.
New
capabilities introduced across the industry. The new 20,000-psi subsea production system is not
just for Gulf of Mexico application. The components are already commercially
available and meet most current regulatory requirements and design guidelines
for other HPHT offshore developments. The recently published third edition of
API 17TR8 provides additional design guidance, with which this system was
proactively designed to already comply. WO
*Mark of Schlumberger
ACKNOWLEDGEMENT
This article
contains elements from OTC paper 32024-MS, which was presented at the Offshore
Technology Conference, May 2–5, 2022.
JOSHUA
POLLAK joined SLB in
2012 as a mechanical engineer in Houston. His career has focused on the design,
building and testing of subsea production system hardware, including trees,
manifolds, wellheads, connectors, and associated tooling. Mr. Pollak has worked
on projects devoted to HPHT technologies, vertical tree development,
digitalization and sustainability efforts.
PARTH PATHAK is a sustainability champion for SLB subsea production systems. He has been with the company for more than 14 years and was a technical leader in development of these HPHT products. He also has been a key contributing member for the industry guidance documents related to this HPHT equipment.