Rotational Molding Informs “Learning Gardens”
Previous Article Next Article
By Jamie Wirkler, Jen Lewin Studio
Boulder, Colorado, USA
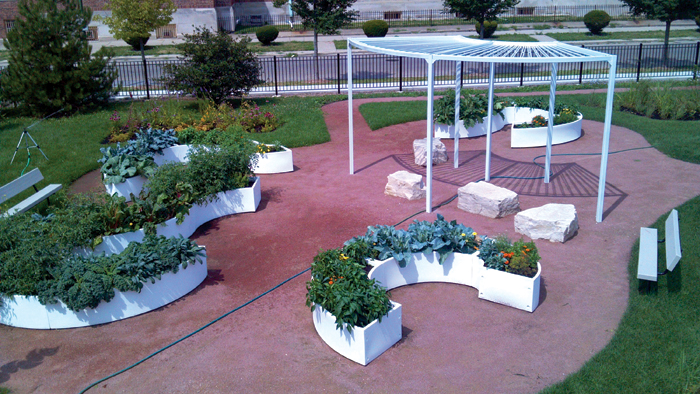
Rotomolded Learning Garden plant beds intalled at the Miles Davis Academy in Chicago.
Note:
The following describes how The Kitchen Community (TKC), a 501(c)(3) non-profit organization, integrated “Learning Gardens” in U.S. schools—using a design concept that took first place in the SPE Rotational Molding Division’s TopCon Design Competition earlier this year.
It was 10 a.m. on a Thursday morning in May 2012. My colleague Peter and I had arrived at Lavizzo Elementary School in the Rosalind neighborhood of Chicago, Illinois. We were counting bolts for one of our first pilot school Learning Garden installations, when we heard, “Pop, pop, pop....” Quickly, Peter jumped up, grabbed me, and said, “Get in the car!” We drove around the backside of the school away from the noise that I had imagined was fireworks. As police cars flew down the street on the north side of the school, we sat in silence still a little shocked from what had just happened.
At two o’clock that afternoon we were confronted with a similar situation 200 meters in the opposite direction of the school, followed by a “crash!” As we emerged from a steel-shipping container that we used for storing rotational-molded Learning Garden beds, more sirens pierced the air and several police cars sped to the scene of a drive-by shooting.
We spoke to the school principal, and I quickly understood that this was a reality of everyday life for these students. Looking around the barren neighborhood, every third or fourth house was boarded up with a big red “X” firmly nailed to its façade. The concrete pad we stood on had circular steel posts that had been cut down to the surface of the concrete. This is where the playground once stood. Adjacent to this cracked concrete pad was the new site of a Learning Garden, complete with permeable pavers, a steel trellis, sitting boulders, and a maze of white curvilinear garden beds.
Purpose of the Gardens
Learning Gardens are outdoor classrooms and experiential play spaces designed to help reverse trends in childhood obesity, improve academic performance, and strengthen communities. The Lavizzo Elementary School’s Learning Garden was built in the spring of 2012 as one of The Kitchen Community’s first pilot schools in Chicago. Today, the Learning Garden at Lavizzo serves as a playground, outdoor classroom, and a way for neighborhood parents and children to grow, harvest, cook, and eat real foods.
Lavizzo Elementary and five other pilot schools were testing their integration into the surrounding communities. After monitoring the Learning Gardens over that summer and seeing their immediate success, we decided to move forward with ten more Learning Gardens in Chicago that fall.
Rotational molding provided us [with] an opportunity to quickly and economically produce actual parts.... Due to the relatively low tooling costs, we could make considerable changes with little financial commitment.—Dan Hatch TKC’s product manager
TKC has since built over 180 Learning Gardens across the USA, positively impacting over 100,000 children in Los Angeles, Denver, and Chicago. Founded by restaurateurs Hugo Matheson and Kimbal Musk as a way to strengthen food culture within communities, TKC’s mission is “Community Through Food,” which can be interpreted in any number of ways. To the founders it reflects the belief that gathering around the table and sharing good food and drink is what connects us as friends, family, and a community.
The Rotomolded Bed
The Learning Garden is made from various steel and plastic components. Jen Lewin, artist and founder of Jen Lewin Studios, conceptualized and designed the original Learning Garden, which was built in Denver at Schmitt Elementary in the fall of 2011. “Part of my goal for the Learning Gardens was heavily biased in my own desire to design elements that engage community through design and art,” says Lewin.
The curvilinear and modular Learning Garden Beds are created using a rotational molding process. Rotational molding is a process by which a steel or aluminum mold is bolted to a carousel arm. After being charged with a specified polymer blend, the mold is sealed and passed through a heating and cooling cycle, spinning biaxially to produce a hollow part with uniform wall thickness. Many playground parts, kayaks, and large storage tanks are rotationally molded, but the process lends itself well to various other applications.
The Learning Garden beds weren’t always rotomolded. At Schmitt Elementary, Lewin designed the beds from powder-coated steel, which worked well for a single school, but its costs were preventative at scale. In order to see real change at scale, Matheson and Musk needed the Learning Garden concept to also be scalable. Looking at freight constraints and manufacturing costs, Lewin and The Kitchen Community sought out advice from the rotational molding community.
“Rotational molding provided us [with] an opportunity to quickly and economically produce actual parts as a startup 501(c)(3),” says Dan Hatch, TKC’s product manager. “Due to the relatively low tooling costs, we could make considerable changes with little financial commitment. Additionally, per-part costs remain low for such a large part, allowing a non-profit like ours to mold and distribute the Garden beds to schools across the country.”
The rotomolded beds feature a single-layer part that involves very little work to install. They’re so lightweight and easy to install that TKC ships a dozen beds to each school and works with students to build the Learning Gardens, setting the modular beds in place and moving ten cubic yards of high-quality growing mix into the containers.
Each Learning Garden bed stands 19 inches (48 cm) above grade and 30 inches (76 cm) wide, with three unique shapes that vary in length from four feet (1.2 m) to over eight feet (2.4 m). The all-white, linear low-density polyethylene (LLDPE) containers feature a mold-stacking feature for shipping that doubles as a varied height drainage basin once soil is added. By varying the height of the drainage feature, air flows freely beneath the beds, which helps to promote an aerobic soil environment for the plants growing within. Each Learning Garden is outfitted on-site with an in-bed irrigation system that schools can connect to their existing irrigation or a nearby spigot.
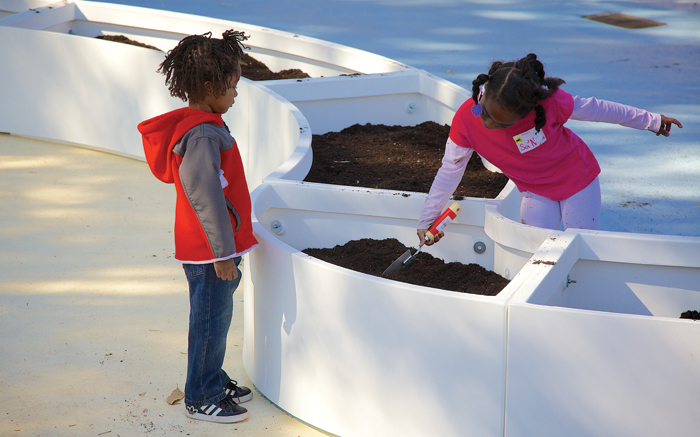
Rotational molding was the affordable solution for creating Learning Gardens… and unique experiences for students (photo courtesy of Laurie Smith).
Containers can be placed directly on existing asphalt or concrete surfacing, helping to keep construction costs lower. In instances where existing surfacing is not available or failing, TKC installs a permeable paver pad for the Learning Garden. In many urban areas, toxic soil is found beneath the surface which prevents schools from having a traditional garden. The Learning Garden fits in just about any schoolyard, so growing in areas where toxic soil lurks beneath is no longer a threat.
Working with Rotational Molding Inc., TKC chose a polymer blend of food-safe LLDPE with an added UV package and a compounded white colorant for year-round outdoor use. LLDPE became the primary choice because it has great freeze-thaw and environmental stress-cracking resistance to face harsh winters and hot summers. Learning Gardens are built to last in outdoor environments in any climate, which makes them a long-term school-gardening solution.
About the author:
Jamie Wirkler began working for The Kitchen Community in January of 2012, transitioning to become the organization’s marketing manager in 2014. In his time at TKC, he helped design, distribute, and build more than 170 Learning Gardens nationwide. He’s a member of the Society of Plastics Engineers and Boulder Young Professionals, and is currently the product and design director at Jen Lewin Studios.
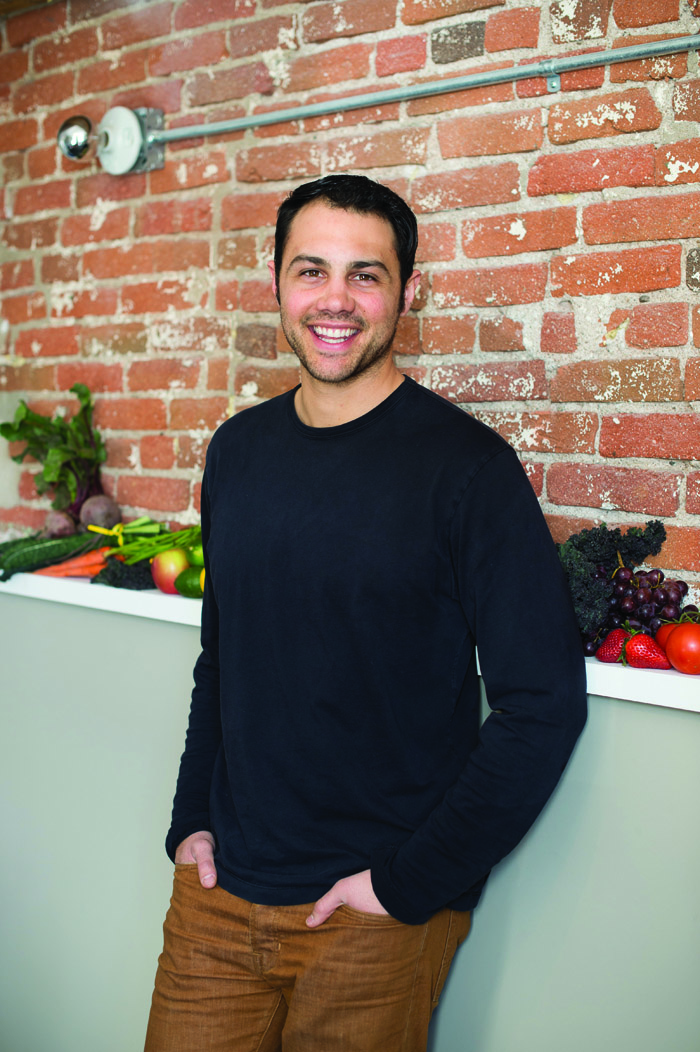
The Author’s Industry Perspective: Designer, Client, and Consumer
Just two years after the Learning Gardens arrived at Lavizzo Elementary, the design was awarded first place in the Society of Plastic Engineers’ Rotational Molding Division’s Design Competition at its TopCon in 2014. The criteria for the award was based on originality, processability, growth potential, beauty/visual appeal, tool building compatibility, use of appropriate materials, and sustainability and environmental impact.
Honored by the award, I flew to Cleveland to speak on behalf of our organization. On the first day of the conference, economist Peter J. Mooney and Jim Bruenig, president of Ball, Bounce and Sport Inc., spoke separately about growth and success within the rotational molding marketplace, echoing 7.2% as the increase in sales for 2014.
In addition to growth, they spoke about innovation, staffing, and making manufacturing exciting again. Rotomolding is a $3.5-billion industry with nearly 2800 rotomolders globally. In the USA, there are a mere 400 rotomolders, and according to Bruenig, it’s become increasingly harder to find and retain staff interested in engineering and manufacturing.
And Mooney noted that rotational molding’s R&D progress was much slower to-market, compared with other plastics processes. Many American rotomolders are small and family-owned. As a result, R&D budgets are nonexistent in many cases. Currently, R&D within the industry is funded in various ways, including earmarked membership dues through trade associations such as SPE or ARM International.
There are only a few instances of how the industry is innovating around materials, workplace development, and processing. Meanwhile, for consumers, there are very limited touch points with the rotomolding industry. How can the industry grow without engagement and interest at the consumer level?
At TopCon 2014, Tom Innis, V.P. of sales and marketing at Lakeland Mold Co., proposed “branding” the industry to connect with the consumer. There’s an entire community of young creators, and in an era of “D.I.Y.,” there’s no reason consumers shouldn’t know about rotomolding. It could be as simple as branding each product with “Powered by Roto,” “RotoMade,” or “Roto Made Local.” Similarly, social media could play a large role in the transformation.
Plastics professionals can do a better job at connecting with the consumer. After all, community is commerce, and if we’re not building a community around rotomolding, it can’t expect to grow as an industry.
Rotational Molding Informs “Learning Gardens”
Previous Article Next Article
By Jamie Wirkler, Jen Lewin Studio
Boulder, Colorado, USA
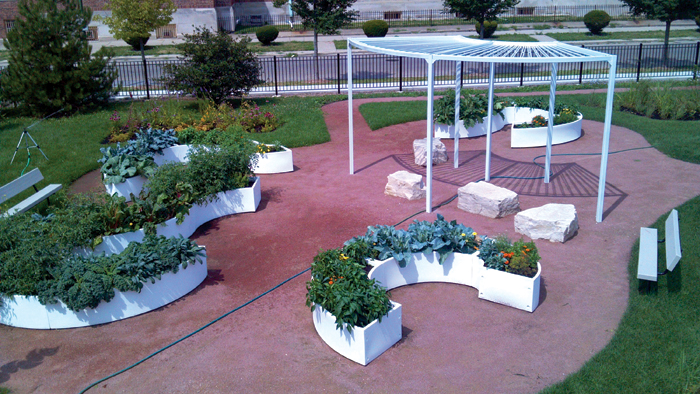
Rotomolded Learning Garden plant beds intalled at the Miles Davis Academy in Chicago.
Note:
The following describes how The Kitchen Community (TKC), a 501(c)(3) non-profit organization, integrated “Learning Gardens” in U.S. schools—using a design concept that took first place in the SPE Rotational Molding Division’s TopCon Design Competition earlier this year.
It was 10 a.m. on a Thursday morning in May 2012. My colleague Peter and I had arrived at Lavizzo Elementary School in the Rosalind neighborhood of Chicago, Illinois. We were counting bolts for one of our first pilot school Learning Garden installations, when we heard, “Pop, pop, pop....” Quickly, Peter jumped up, grabbed me, and said, “Get in the car!” We drove around the backside of the school away from the noise that I had imagined was fireworks. As police cars flew down the street on the north side of the school, we sat in silence still a little shocked from what had just happened.
At two o’clock that afternoon we were confronted with a similar situation 200 meters in the opposite direction of the school, followed by a “crash!” As we emerged from a steel-shipping container that we used for storing rotational-molded Learning Garden beds, more sirens pierced the air and several police cars sped to the scene of a drive-by shooting.
We spoke to the school principal, and I quickly understood that this was a reality of everyday life for these students. Looking around the barren neighborhood, every third or fourth house was boarded up with a big red “X” firmly nailed to its façade. The concrete pad we stood on had circular steel posts that had been cut down to the surface of the concrete. This is where the playground once stood. Adjacent to this cracked concrete pad was the new site of a Learning Garden, complete with permeable pavers, a steel trellis, sitting boulders, and a maze of white curvilinear garden beds.
Purpose of the Gardens
Learning Gardens are outdoor classrooms and experiential play spaces designed to help reverse trends in childhood obesity, improve academic performance, and strengthen communities. The Lavizzo Elementary School’s Learning Garden was built in the spring of 2012 as one of The Kitchen Community’s first pilot schools in Chicago. Today, the Learning Garden at Lavizzo serves as a playground, outdoor classroom, and a way for neighborhood parents and children to grow, harvest, cook, and eat real foods.
Lavizzo Elementary and five other pilot schools were testing their integration into the surrounding communities. After monitoring the Learning Gardens over that summer and seeing their immediate success, we decided to move forward with ten more Learning Gardens in Chicago that fall.
Rotational molding provided us [with] an opportunity to quickly and economically produce actual parts.... Due to the relatively low tooling costs, we could make considerable changes with little financial commitment.—Dan Hatch TKC’s product manager
TKC has since built over 180 Learning Gardens across the USA, positively impacting over 100,000 children in Los Angeles, Denver, and Chicago. Founded by restaurateurs Hugo Matheson and Kimbal Musk as a way to strengthen food culture within communities, TKC’s mission is “Community Through Food,” which can be interpreted in any number of ways. To the founders it reflects the belief that gathering around the table and sharing good food and drink is what connects us as friends, family, and a community.
The Rotomolded Bed
The Learning Garden is made from various steel and plastic components. Jen Lewin, artist and founder of Jen Lewin Studios, conceptualized and designed the original Learning Garden, which was built in Denver at Schmitt Elementary in the fall of 2011. “Part of my goal for the Learning Gardens was heavily biased in my own desire to design elements that engage community through design and art,” says Lewin.
The curvilinear and modular Learning Garden Beds are created using a rotational molding process. Rotational molding is a process by which a steel or aluminum mold is bolted to a carousel arm. After being charged with a specified polymer blend, the mold is sealed and passed through a heating and cooling cycle, spinning biaxially to produce a hollow part with uniform wall thickness. Many playground parts, kayaks, and large storage tanks are rotationally molded, but the process lends itself well to various other applications.
The Learning Garden beds weren’t always rotomolded. At Schmitt Elementary, Lewin designed the beds from powder-coated steel, which worked well for a single school, but its costs were preventative at scale. In order to see real change at scale, Matheson and Musk needed the Learning Garden concept to also be scalable. Looking at freight constraints and manufacturing costs, Lewin and The Kitchen Community sought out advice from the rotational molding community.
“Rotational molding provided us [with] an opportunity to quickly and economically produce actual parts as a startup 501(c)(3),” says Dan Hatch, TKC’s product manager. “Due to the relatively low tooling costs, we could make considerable changes with little financial commitment. Additionally, per-part costs remain low for such a large part, allowing a non-profit like ours to mold and distribute the Garden beds to schools across the country.”
The rotomolded beds feature a single-layer part that involves very little work to install. They’re so lightweight and easy to install that TKC ships a dozen beds to each school and works with students to build the Learning Gardens, setting the modular beds in place and moving ten cubic yards of high-quality growing mix into the containers.
Each Learning Garden bed stands 19 inches (48 cm) above grade and 30 inches (76 cm) wide, with three unique shapes that vary in length from four feet (1.2 m) to over eight feet (2.4 m). The all-white, linear low-density polyethylene (LLDPE) containers feature a mold-stacking feature for shipping that doubles as a varied height drainage basin once soil is added. By varying the height of the drainage feature, air flows freely beneath the beds, which helps to promote an aerobic soil environment for the plants growing within. Each Learning Garden is outfitted on-site with an in-bed irrigation system that schools can connect to their existing irrigation or a nearby spigot.
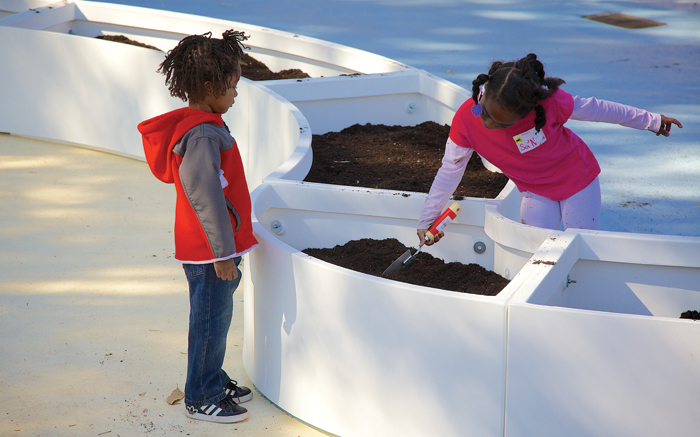
Rotational molding was the affordable solution for creating Learning Gardens… and unique experiences for students (photo courtesy of Laurie Smith).
Containers can be placed directly on existing asphalt or concrete surfacing, helping to keep construction costs lower. In instances where existing surfacing is not available or failing, TKC installs a permeable paver pad for the Learning Garden. In many urban areas, toxic soil is found beneath the surface which prevents schools from having a traditional garden. The Learning Garden fits in just about any schoolyard, so growing in areas where toxic soil lurks beneath is no longer a threat.
Working with Rotational Molding Inc., TKC chose a polymer blend of food-safe LLDPE with an added UV package and a compounded white colorant for year-round outdoor use. LLDPE became the primary choice because it has great freeze-thaw and environmental stress-cracking resistance to face harsh winters and hot summers. Learning Gardens are built to last in outdoor environments in any climate, which makes them a long-term school-gardening solution.
About the author:
Jamie Wirkler began working for The Kitchen Community in January of 2012, transitioning to become the organization’s marketing manager in 2014. In his time at TKC, he helped design, distribute, and build more than 170 Learning Gardens nationwide. He’s a member of the Society of Plastics Engineers and Boulder Young Professionals, and is currently the product and design director at Jen Lewin Studios.
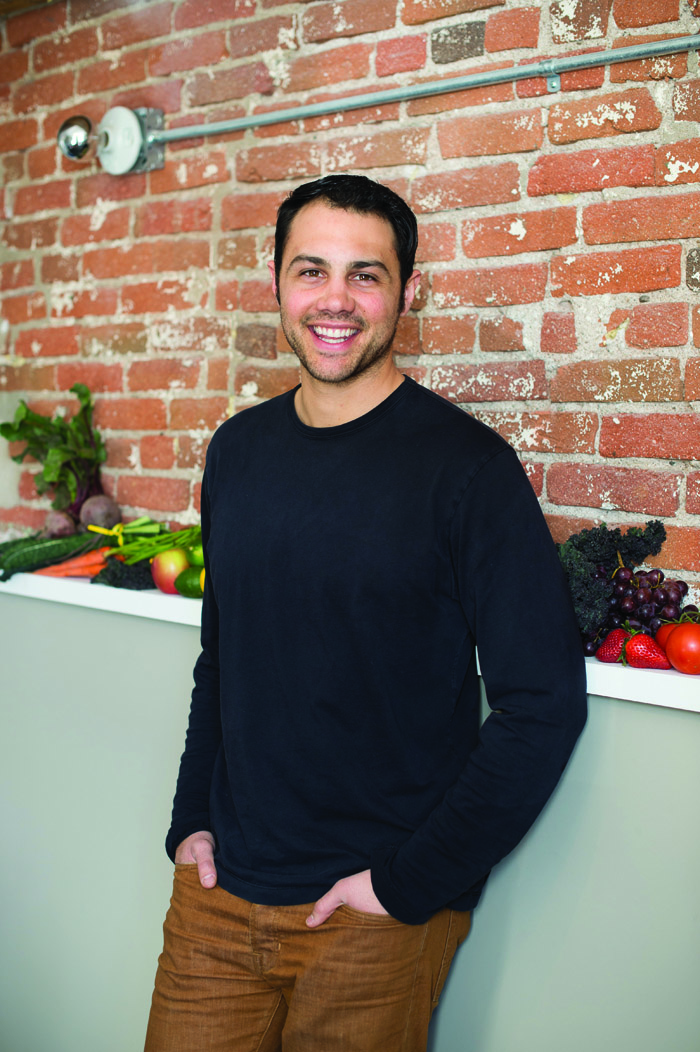
Rotational Molding Informs “Learning Gardens
Just two years after the Learning Gardens arrived at Lavizzo Elementary, the design was awarded first place in the Society of Plastic Engineers’ Rotational Molding Division’s Design Competition at its TopCon in 2014. The criteria for the award was based on originality, processability, growth potential, beauty/visual appeal, tool building compatibility, use of appropriate materials, and sustainability and environmental impact.
Honored by the award, I flew to Cleveland to speak on behalf of our organization. On the first day of the conference, economist Peter J. Mooney and Jim Bruenig, president of Ball, Bounce and Sport Inc., spoke separately about growth and success within the rotational molding marketplace, echoing 7.2% as the increase in sales for 2014.
In addition to growth, they spoke about innovation, staffing, and making manufacturing exciting again. Rotomolding is a $3.5-billion industry with nearly 2800 rotomolders globally. In the USA, there are a mere 400 rotomolders, and according to Bruenig, it’s become increasingly harder to find and retain staff interested in engineering and manufacturing.
And Mooney noted that rotational molding’s R&D progress was much slower to-market, compared with other plastics processes. Many American rotomolders are small and family-owned. As a result, R&D budgets are nonexistent in many cases. Currently, R&D within the industry is funded in various ways, including earmarked membership dues through trade associations such as SPE or ARM International.
There are only a few instances of how the industry is innovating around materials, workplace development, and processing. Meanwhile, for consumers, there are very limited touch points with the rotomolding industry. How can the industry grow without engagement and interest at the consumer level?
At TopCon 2014, Tom Innis, V.P. of sales and marketing at Lakeland Mold Co., proposed “branding” the industry to connect with the consumer. There’s an entire community of young creators, and in an era of “D.I.Y.,” there’s no reason consumers shouldn’t know about rotomolding. It could be as simple as branding each product with “Powered by Roto,” “RotoMade,” or “Roto Made Local.” Similarly, social media could play a large role in the transformation.
Plastics professionals can do a better job at connecting with the consumer. After all, community is commerce, and if we’re not building a community around rotomolding, it can’t expect to grow as an industry.
Rotational Molding Informs “Learning Gardens”
Previous Article Next Article
By Jamie Wirkler, Jen Lewin Studio
Boulder, Colorado, USA
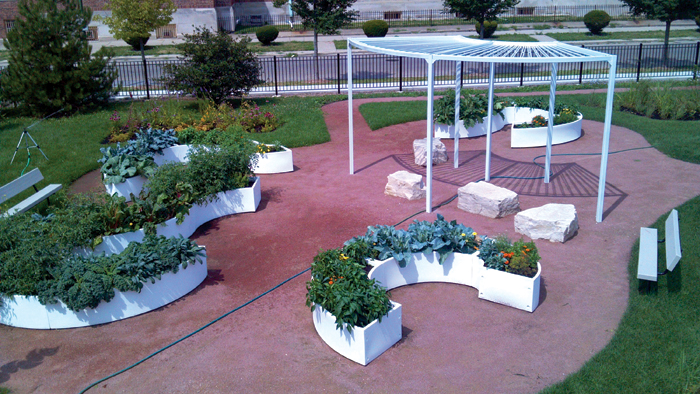
Rotomolded Learning Garden plant beds intalled at the Miles Davis Academy in Chicago.
Note:
The following describes how The Kitchen Community (TKC), a 501(c)(3) non-profit organization, integrated “Learning Gardens” in U.S. schools—using a design concept that took first place in the SPE Rotational Molding Division’s TopCon Design Competition earlier this year.
It was 10 a.m. on a Thursday morning in May 2012. My colleague Peter and I had arrived at Lavizzo Elementary School in the Rosalind neighborhood of Chicago, Illinois. We were counting bolts for one of our first pilot school Learning Garden installations, when we heard, “Pop, pop, pop....” Quickly, Peter jumped up, grabbed me, and said, “Get in the car!” We drove around the backside of the school away from the noise that I had imagined was fireworks. As police cars flew down the street on the north side of the school, we sat in silence still a little shocked from what had just happened.
At two o’clock that afternoon we were confronted with a similar situation 200 meters in the opposite direction of the school, followed by a “crash!” As we emerged from a steel-shipping container that we used for storing rotational-molded Learning Garden beds, more sirens pierced the air and several police cars sped to the scene of a drive-by shooting.
We spoke to the school principal, and I quickly understood that this was a reality of everyday life for these students. Looking around the barren neighborhood, every third or fourth house was boarded up with a big red “X” firmly nailed to its façade. The concrete pad we stood on had circular steel posts that had been cut down to the surface of the concrete. This is where the playground once stood. Adjacent to this cracked concrete pad was the new site of a Learning Garden, complete with permeable pavers, a steel trellis, sitting boulders, and a maze of white curvilinear garden beds.
Purpose of the Gardens
Learning Gardens are outdoor classrooms and experiential play spaces designed to help reverse trends in childhood obesity, improve academic performance, and strengthen communities. The Lavizzo Elementary School’s Learning Garden was built in the spring of 2012 as one of The Kitchen Community’s first pilot schools in Chicago. Today, the Learning Garden at Lavizzo serves as a playground, outdoor classroom, and a way for neighborhood parents and children to grow, harvest, cook, and eat real foods.
Lavizzo Elementary and five other pilot schools were testing their integration into the surrounding communities. After monitoring the Learning Gardens over that summer and seeing their immediate success, we decided to move forward with ten more Learning Gardens in Chicago that fall.
Rotational molding provided us [with] an opportunity to quickly and economically produce actual parts.... Due to the relatively low tooling costs, we could make considerable changes with little financial commitment.—Dan Hatch TKC’s product manager
TKC has since built over 180 Learning Gardens across the USA, positively impacting over 100,000 children in Los Angeles, Denver, and Chicago. Founded by restaurateurs Hugo Matheson and Kimbal Musk as a way to strengthen food culture within communities, TKC’s mission is “Community Through Food,” which can be interpreted in any number of ways. To the founders it reflects the belief that gathering around the table and sharing good food and drink is what connects us as friends, family, and a community.
The Rotomolded Bed
The Learning Garden is made from various steel and plastic components. Jen Lewin, artist and founder of Jen Lewin Studios, conceptualized and designed the original Learning Garden, which was built in Denver at Schmitt Elementary in the fall of 2011. “Part of my goal for the Learning Gardens was heavily biased in my own desire to design elements that engage community through design and art,” says Lewin.
The curvilinear and modular Learning Garden Beds are created using a rotational molding process. Rotational molding is a process by which a steel or aluminum mold is bolted to a carousel arm. After being charged with a specified polymer blend, the mold is sealed and passed through a heating and cooling cycle, spinning biaxially to produce a hollow part with uniform wall thickness. Many playground parts, kayaks, and large storage tanks are rotationally molded, but the process lends itself well to various other applications.
The Learning Garden beds weren’t always rotomolded. At Schmitt Elementary, Lewin designed the beds from powder-coated steel, which worked well for a single school, but its costs were preventative at scale. In order to see real change at scale, Matheson and Musk needed the Learning Garden concept to also be scalable. Looking at freight constraints and manufacturing costs, Lewin and The Kitchen Community sought out advice from the rotational molding community.
“Rotational molding provided us [with] an opportunity to quickly and economically produce actual parts as a startup 501(c)(3),” says Dan Hatch, TKC’s product manager. “Due to the relatively low tooling costs, we could make considerable changes with little financial commitment. Additionally, per-part costs remain low for such a large part, allowing a non-profit like ours to mold and distribute the Garden beds to schools across the country.”
The rotomolded beds feature a single-layer part that involves very little work to install. They’re so lightweight and easy to install that TKC ships a dozen beds to each school and works with students to build the Learning Gardens, setting the modular beds in place and moving ten cubic yards of high-quality growing mix into the containers.
Each Learning Garden bed stands 19 inches (48 cm) above grade and 30 inches (76 cm) wide, with three unique shapes that vary in length from four feet (1.2 m) to over eight feet (2.4 m). The all-white, linear low-density polyethylene (LLDPE) containers feature a mold-stacking feature for shipping that doubles as a varied height drainage basin once soil is added. By varying the height of the drainage feature, air flows freely beneath the beds, which helps to promote an aerobic soil environment for the plants growing within. Each Learning Garden is outfitted on-site with an in-bed irrigation system that schools can connect to their existing irrigation or a nearby spigot.
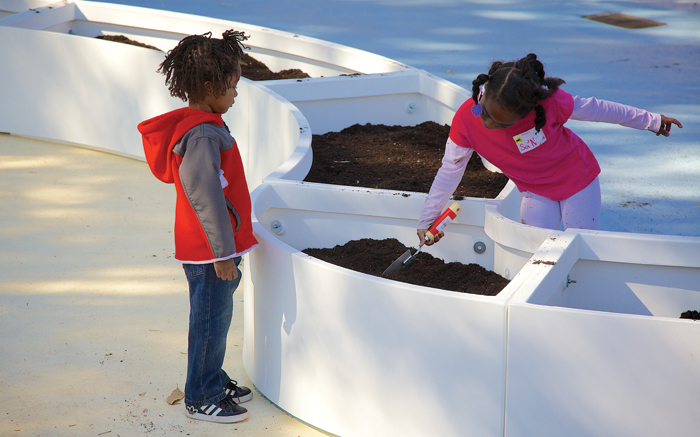
Rotational molding was the affordable solution for creating Learning Gardens… and unique experiences for students (photo courtesy of Laurie Smith).
Containers can be placed directly on existing asphalt or concrete surfacing, helping to keep construction costs lower. In instances where existing surfacing is not available or failing, TKC installs a permeable paver pad for the Learning Garden. In many urban areas, toxic soil is found beneath the surface which prevents schools from having a traditional garden. The Learning Garden fits in just about any schoolyard, so growing in areas where toxic soil lurks beneath is no longer a threat.
Working with Rotational Molding Inc., TKC chose a polymer blend of food-safe LLDPE with an added UV package and a compounded white colorant for year-round outdoor use. LLDPE became the primary choice because it has great freeze-thaw and environmental stress-cracking resistance to face harsh winters and hot summers. Learning Gardens are built to last in outdoor environments in any climate, which makes them a long-term school-gardening solution.
About the author:
Jamie Wirkler began working for The Kitchen Community in January of 2012, transitioning to become the organization’s marketing manager in 2014. In his time at TKC, he helped design, distribute, and build more than 170 Learning Gardens nationwide. He’s a member of the Society of Plastics Engineers and Boulder Young Professionals, and is currently the product and design director at Jen Lewin Studios.
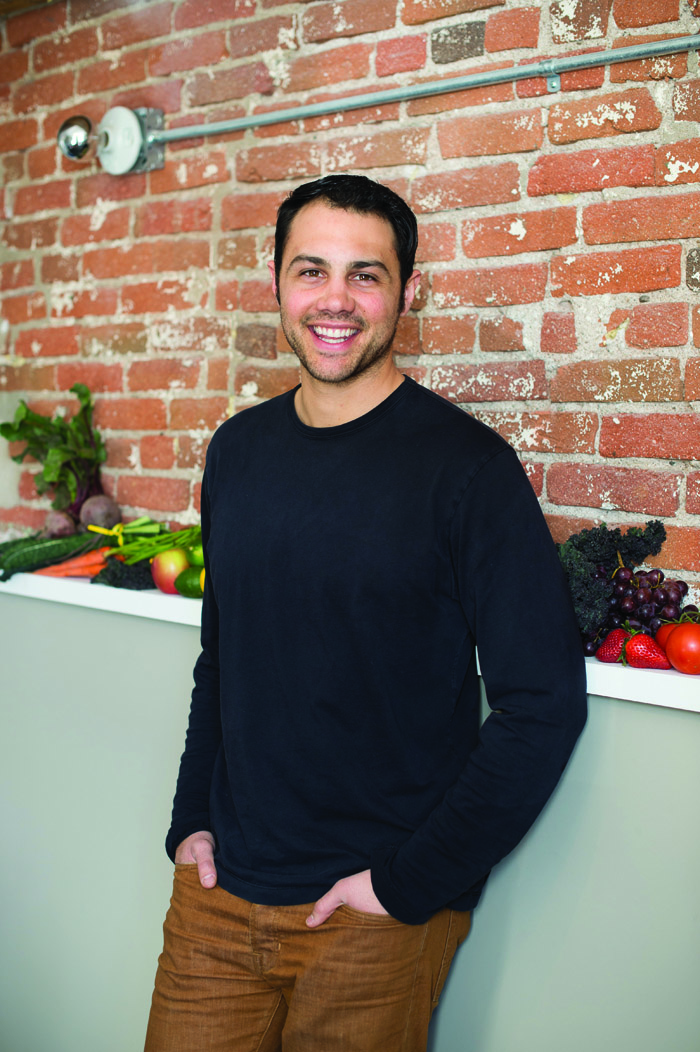
Rotational Molding Informs “Learning Gardens
Just two years after the Learning Gardens arrived at Lavizzo Elementary, the design was awarded first place in the Society of Plastic Engineers’ Rotational Molding Division’s Design Competition at its TopCon in 2014. The criteria for the award was based on originality, processability, growth potential, beauty/visual appeal, tool building compatibility, use of appropriate materials, and sustainability and environmental impact.
Honored by the award, I flew to Cleveland to speak on behalf of our organization. On the first day of the conference, economist Peter J. Mooney and Jim Bruenig, president of Ball, Bounce and Sport Inc., spoke separately about growth and success within the rotational molding marketplace, echoing 7.2% as the increase in sales for 2014.
In addition to growth, they spoke about innovation, staffing, and making manufacturing exciting again. Rotomolding is a $3.5-billion industry with nearly 2800 rotomolders globally. In the USA, there are a mere 400 rotomolders, and according to Bruenig, it’s become increasingly harder to find and retain staff interested in engineering and manufacturing.
And Mooney noted that rotational molding’s R&D progress was much slower to-market, compared with other plastics processes. Many American rotomolders are small and family-owned. As a result, R&D budgets are nonexistent in many cases. Currently, R&D within the industry is funded in various ways, including earmarked membership dues through trade associations such as SPE or ARM International.
There are only a few instances of how the industry is innovating around materials, workplace development, and processing. Meanwhile, for consumers, there are very limited touch points with the rotomolding industry. How can the industry grow without engagement and interest at the consumer level?
At TopCon 2014, Tom Innis, V.P. of sales and marketing at Lakeland Mold Co., proposed “branding” the industry to connect with the consumer. There’s an entire community of young creators, and in an era of “D.I.Y.,” there’s no reason consumers shouldn’t know about rotomolding. It could be as simple as branding each product with “Powered by Roto,” “RotoMade,” or “Roto Made Local.” Similarly, social media could play a large role in the transformation.
Plastics professionals can do a better job at connecting with the consumer. After all, community is commerce, and if we’re not building a community around rotomolding, it can’t expect to grow as an industry.