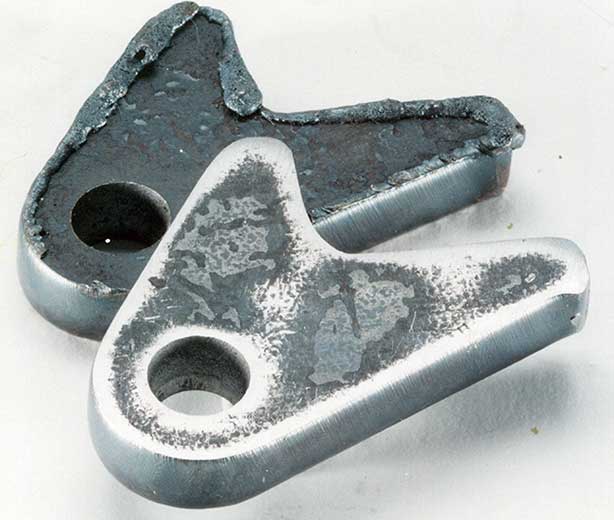
Dross on parts can be controlled by changing various cutting parameters.
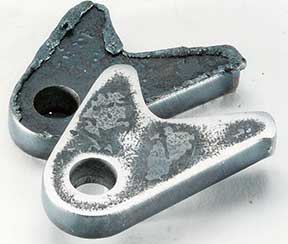
Dross on parts can be controlled by changing various cutting parameters.
Every time I do a laser operator training class I begin to sound like a broken record.
When we start to discuss making machine adjustments to eliminate dross or undesirable edge-quality conditions, I drill this statement into the class attendees: If your cutting lens' focal point is incorrect, just about every single cutting parameter will change to compensate for this it, and it should have been set up properly as step one when the production order was done.
I can't stress enough the importance of making sure your laser's FOCUS is correct before you make any cutting parameter changes. I will repeat myself constantly over and over during the training session. So when troubleshooting a problem you need to FOCUS on the problem to resolve it. Of course, the key word here is FOCUS. It's such a simple thing that is often overlooked, and the best part is that it's a FREE fix.
Every week as I travel from one factory to another I see poor quality, dross laden parts and manufacturers having elaborate grinding stations or extra personnel to take care of this problem. All because the laser operator is always behind on orders and has no time to cleanup his drossy parts.
Don’t get me wrong, the laser is constantly running, so he must be busy, right? Well the truth is that the laser is capable of giving a very precise high-quality edge if it's maintained correctly, and if the operator sets the FOCUS correctly. By doing this, there should be little grinding needed, if at all.
If the FOCUS is correct, the laser can cut at maximum feed rates, speeding up cycle times and reducing part costs. AGAIN this fix is free, with no added costs for grinders, grinding discs, labor, factory floor space and added time to build the product. It’s a laser, and that precise edge quality is exactly why the technology was invested in, so why settle for less.
Usually during the material processing portion of training laser operators, I have the opportunity to work with personnel that might already have knowledge of the machine or have run a different brand of laser at another company for years.
We usually start discussing the interaction of the laser beam with the material with heavy discussion on the FOCUS, because it's the most important parameter, and the first item adjusted when setting up a production run.
We then follow up with cutting a part with the manufacturer's recommended cutting parameters and normally get a drossy part. I prefer to use the manufacturer's suggested parameters, because I know that the laser's focus is usually incorrect, and we should only have one adjustment to make to obtain a quality edge.
So the first question is where do we start making adjustments. The experienced operators usually jump into the conversation with the comment that the manufacturer's parameters never work. Then they suggest gas-pressure and feed-rate adjustments. They're good answers, but not for the first adjustment, FOCUS comes first, and once the FOCUS is correct, then we can adjust the other parameters if required.
What else causes dross?
So besides the focus, what else causes dross? Lets begin by looking at the interaction between the 10.6-micron wavelength of the CO2-laser coupling to the material we're processing, and assume that the laser-beam mode is symmetrical, and our beam alignment is perfectly centered over our cutting lens to simplify things.
Of course, the laser melts and vaporizes material, which can also leave behind dross that includes metal oxides and impurities from the material being processed. If the dross is not expelled out through the kerf properly, it will adhere to the bottom side of the part.
If mild steel is processed using oxygen, we get the unavoidable oxidizing reaction in the process caused by the oxygen. As you probably know, mild steel melts at a much lower temperature than the laser beam can produce. If we overheat the material, we get dross. If the power is too low, we get dross.
Now there is a significant difference between the two types of dross. When the material is overheated, the dross adheres itself tightly to the part's surface and is re-melted back into it, and it's difficult to remove. Usually a grinder is required. To correct this, first verify that the FOCUS is correct. Then increase the feed rate or reduce the amount of oxygen pressure or lower the overall power being used.
Conversely, if the power is low, the molten material from the kerf forms small beads on the exiting surface and would wipe off unless the power level is excessively low. Then it might form a strip of dross that you could pull off with your hands in one long strip. A grinder is normally not required for this. To correct this, verify that the FOCUS is correct, then increase the gas pressure or increase the power. Or ultimately you might have to reduce the feed rate.
If you have a higher powered laser, a common solution is to process mild steel with high pressure nitrogen, removing oxygen from the equation. Although the cut quality will improve, the cutting efficiency in certain material thickness will be reduced, because of the lack of energy generated from an exothermic oxidation reaction that oxygen gives you.
However if thin-mild steel is being processed, we can actually increase our speed for the exact same reason. Now dross from this process comes in two forms as well. If the material is overheated, we get dross that looks like black icicles hanging from the bottom edge. To correct this, verify that the FOCUS is correct. Then increase the gas pressure or decrease the power. Or ultimately increase the feed rate.
If we use power that's too low, we get dross that will be very fine in thickness and slanted in the opposite direction of the cut travel. The dross will be very sharp and pointed like needles and silvery in color. To correct this, verify your FOCUS is correct then decrease the gas pressure or increase the power. Or ultimately you might have to reduce your feed rate.
Processing stainless and aluminum will need similar adjustments as cutting mild steel with nitrogen.
Material quality
Laser processing is more sensitive to material quality than any other process. Different material compositions will melt at different temperatures affecting the cut settings for cutting process.
Hot-rolled steel presents challenges when cutting because of the surface scale. Surface impurities melt into the metal, creating hot pockets or gouges. If the material surface is not smooth, the laser beam will scatter on the multitude of surfaces it contacts. Remember a small percentage of light will scatter on each surface it encounters diffusing the laser beam. In a general sense, steel should be clean, pickled and oiled for better results. Of course this will have effect on the dross.
Material composition
Impurities in low-grade steel are highly reactive in the thermal process when using oxygen as the assist gas. Inconsistent material composition affects laser processing more dramatically than it does other processing methods.
Percentages of magnesium, silicone, and carbon content all affect the material combustion. For example, higher carbon steels that are often used as structural steel will vaporize quickly when they come into contact with the laser beam.
Compared to more homogenous materials, carbon steels may contain a wide range of elements that have different melting points. During the thermal process, random reactions can occur because of composition variance, and the surface condition of the material. These surface conditions include scale, rust, and surface impurities such as paint from markers, etc. Again, this will have effect on the dross.
Compare material certifications from material that cuts well with material that the operator really struggles with, and you can develop an acceptable range for the compositions.
Dross is also influenced by conductivity and the viscosity of the molten metal in a liquid state. The surface tension of molten material affects the degree of dross that adheres to the bottom edge of the cut. If the viscosity is thin, the dross will blow away. However, if it's thick, it will tend to cling to the material and usually transfers its heat back into the part. In such cases, secondary operations may be required to remove the dross.
Now the challenge of cutting thicker plate is limited by heat conductivity, surface reflection at 10.6 microns, the vaporization point of alloys, the percentages of alloys, surface tension of molten materials and part geometry. As material thickness increases, the chances of a blowout or thermal runaway also increases.
Part Geometry and software programming
Certain part geometries are affected more than others by the thermal process. For example, sharp corners or areas smaller than material thickness will absorb more heat, and consequently cause thermal runaway or cause violent reactions like blowouts unless thought is put into the part's program.
Generally, the more complicated the part geometry, the more difficult it is to maintain constant cutting speeds. Often speed and productivity are compromised when cutting shapes with varying features and angles. Changing the laser's frequency or duty cycle, rather than using a continuous wave, can reduce thermal problems. Of course this will have effect on the dross.
There is much that can affect getting dross, such as material composition, material quality, assist-gas quality, software programming, part geometry, cutting-nozzle diameter, and on thicker material, a one PSI change in assist-gas pressure.
Remember, we started this article assuming the laser was running perfectly. We also assumed the lens was perfect. Also note that cutting aluminum and stainless steel requires a different mind set and normally an opposite adjustment from mild steel processed with oxygen.
Dross seems like a very basic problem, but I'll let you be the judge.