
Photograph shows Wila HD HU-134 Heavy Duty Punch Holder being stored in Press Brake Productivity ToolStation. Note the E2M Easy To Move roller bearings on the tang for fast, safe and easy loading and unloading.
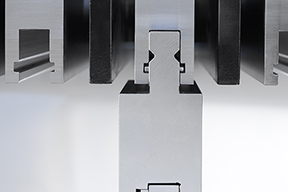
Photograph shows Wila HD HU-134 Heavy Duty Punch Holder being stored in Press Brake Productivity ToolStation. Note the E2M Easy To Move roller bearings on the tang for fast, safe and easy loading and unloading.
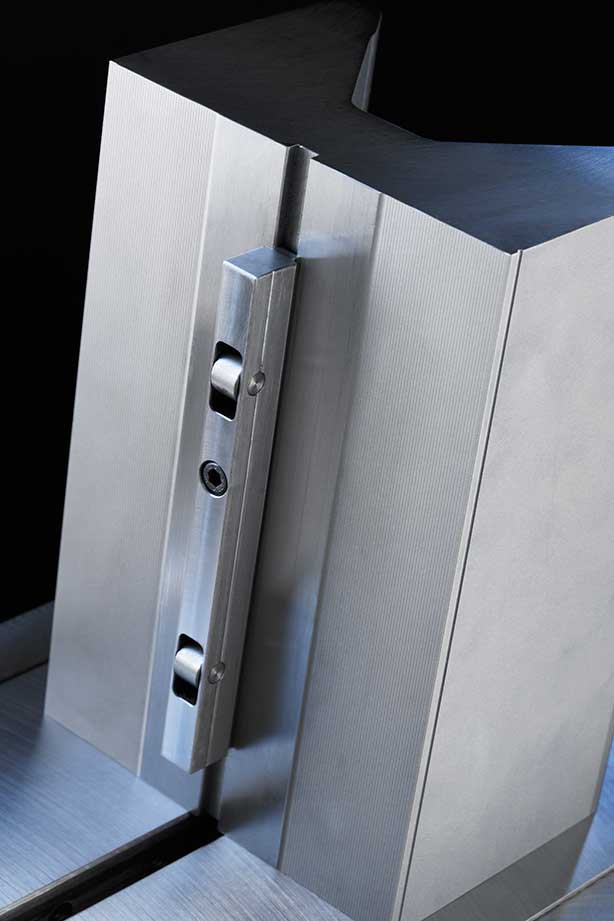
Photograph shows a Wila HD Die with the E2M Easy To Move roller bearings mounted in the tang for fast, safe, and easy loading and unloading.
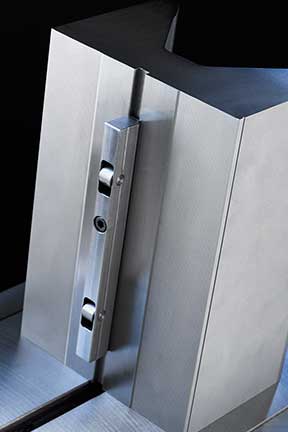
Photograph shows a Wila HD Die with the E2M Easy To Move roller bearings mounted in the tang for fast, safe, and easy loading and unloading.
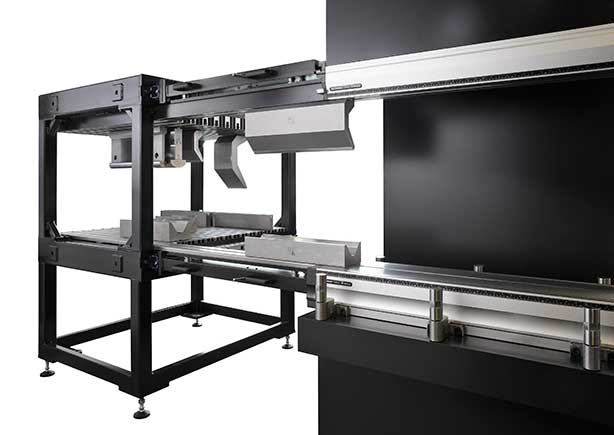
Photograph shows the entire Wila New Standard HD System including tooling, clamping system, crowning system with optional pillars, and the Press Brake Productivity ToolStation.
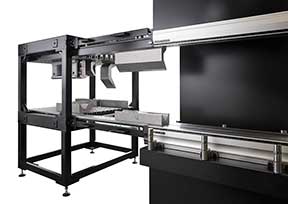
Photograph shows the entire Wila New Standard HD System including tooling, clamping system, crowning system with optional pillars, and the Press Brake Productivity ToolStation.
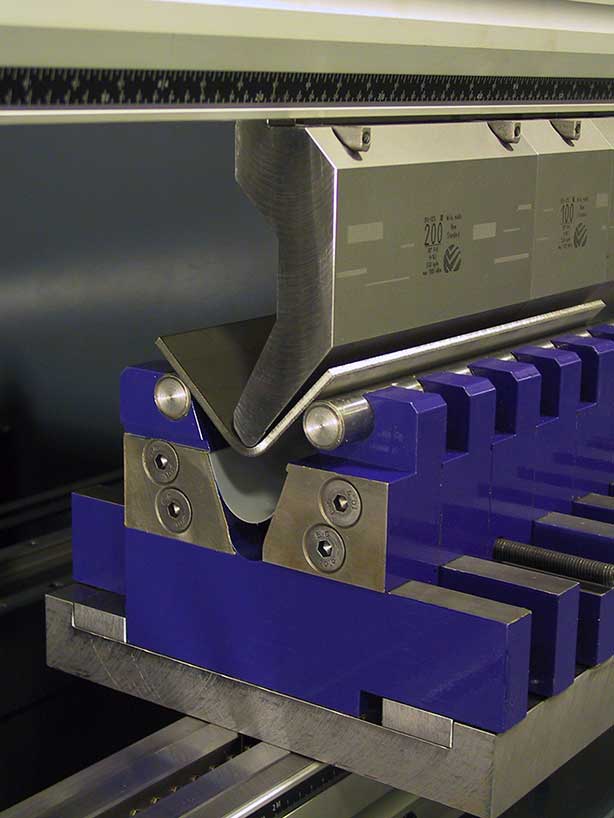
Photograph shows Wila Model B Multi-V Die with BIU-025 Gooseneck Punch being used to bend a piece of 0.188 in. hot rolled steel.

Photograph shows Wila Model B Multi-V Die with BIU-025 Gooseneck Punch being used to bend a piece of 0.188 in. hot rolled steel.
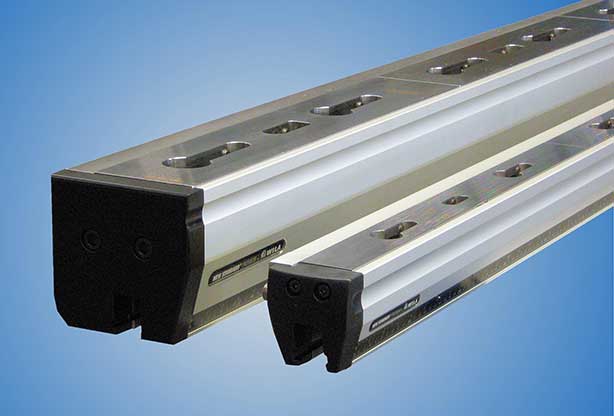
Photograph shows a visual comparison between the size of the new New Standard “HD’ Clamping System and the popular NSCL-II-HC/UPB Clamping system.
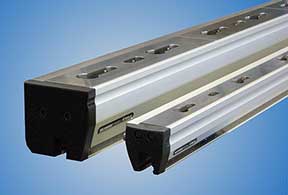
Photograph shows a visual comparison between the size of the new New Standard “HD’ Clamping System and the popular NSCL-II-HC/UPB Clamping system.
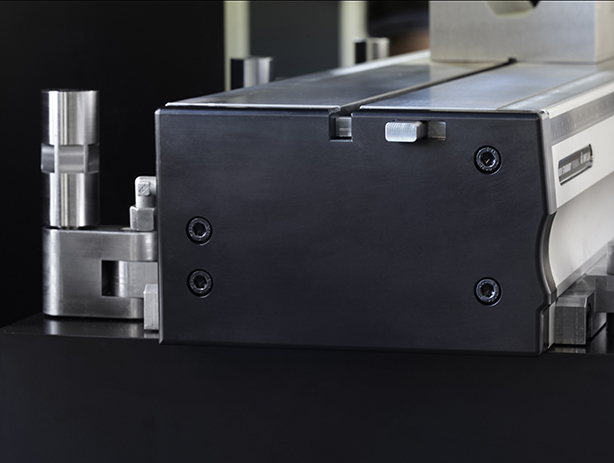
Photograph shows a Wila Crowning System with optional pillars.

Photograph shows a Wila Crowning System with optional pillars.
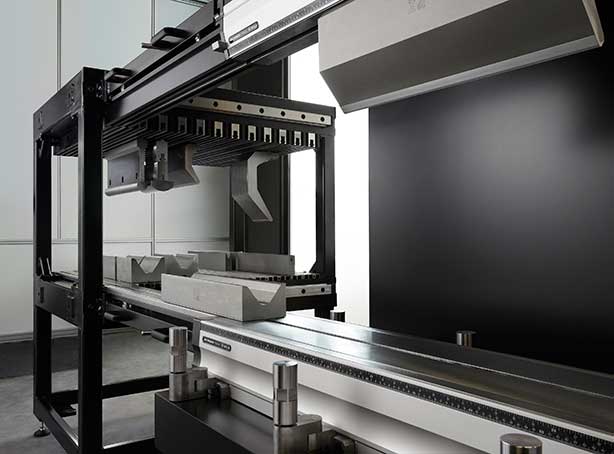
Photograph shows Wila’s new HD Press Brake Productivity ToolStation with loading and unloading arms.
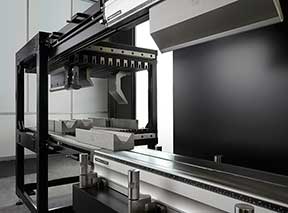
Photograph shows Wila’s new HD Press Brake Productivity ToolStation with loading and unloading arms.
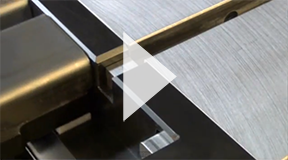
Wila's ToolStation Demonstration.
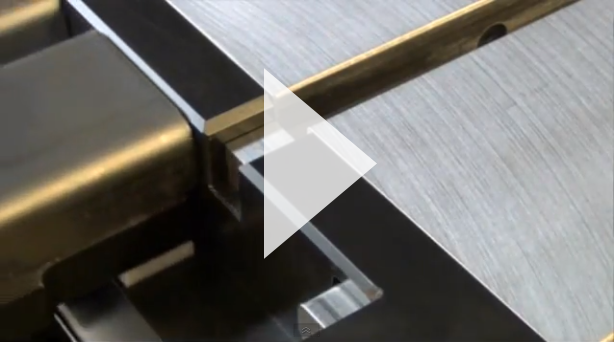
Wila's ToolStation Demonstration.
Bending thick plate steel has never been an easy task. Fortunately, new tooling offers a brighter future.
Bending plate generally requires large expensive press brakes that are capable of delivering high tonnage levels, tooling that is very long, heavy, and difficult to load and unload, and quite often multiple press brake operators to handle the large heavy sheets. And needless to say, going from one set-up to another is normally anything but fast.
Most plate fabricators have come to accept these conditions as being unavoidable realities of their business and have done their best to work around them.
To change this, Wila has dedicated a tremendous amount of resources to developing new products that maximize productivity, finished part quality, and most importantly, operator safety for fabricators that bend these thick heavy materials.
Multi-V dies
One of Wila’s earliest product introductions for plate fabricators is their full line of Manually Adjustable Multi-V Dies. They can be changed from one V-opening to another in a matter of minutes by sliding out a simple set of spacer bars and replacing them with another set and then locking them in place with two set screws. That’s all there is to an average setup!
They come with hardened rollers on the shoulders that are replaceable. These rollers provide virtually unlimited life, maximum long term accuracy, reduced part marking and reduced tonnage requirements.
Fabricators that are bending some of today’s newer high-tensile-strength materials such as Hardox and Weldox for example, have found the ability of Wila Multi-V Dies to make acute bends extremely beneficial in compensating for the high levels of springback in these materials.
Possibly the most desirable features of Wila’s Manually Adjustable Multi-V Dies are their adjustability and ability to handle a wide range of plate bending applications. They rarely need to be removed from the press brake. This can virtually eliminate the need for press brake and forklift operators to handle the heavy, awkward, and often dangerous large single-V dies and 4-way dies that are normally used to bend thick-plate materials. And that alone provides for an invaluable measure of safety.
Wila debuts new standard HD heavy duty system
Last year Wila introduced its new New Standard HD Heavy Duty System. This system is the first of its type and consists of tooling, clamping, crowning and lower tool holder systems that are designed to handle the extremely high tonnage levels and harsh demanding conditions that are common to bending thick plate materials. It also includes an innovative Press Brake Productivity ToolStation that is used for tooling storage as well as easy tool loading and unloading. Let’s look at the individual features of each of these components.
New standard HD tooling system
Any new tooling systems that is designed for bending thick plate materials must be exceptionally strong, wear resistant and most importantly, safe to use. Recognizing the need to expand its product line to handle thick plate materials, Wila added New Standard HD Straight Punches that have 0.236 in. and 0.492 in. tip radii. They have also added a new punch holder and a series of large radius punch inserts ranging from 0.236 in. to 1.969 in. tip radii.
The straight punches, gooseneck punch and punch holder are available with a new Wila innovation known as E2M Easy To Move roller bearings. The E2M roller bearings (patent pending) are placed in the tang of the new punches and punch holders. When used with the new Wila New Standard HD Clamping System, they align with a slot in the clamping system, which makes them very fast, safe and easy to load and unload when used in conjunction with the new standard Press Brake Productivity ToolStation, which will be explained later in this article.
Another innovative feature that Wila introduced with its New Standard HD Punches includes an E2M roller bearing that supports the back of heavy gooseneck style punches against the clamping system. This feature prevents them from hanging at an angle in the clamping system, thus aiding fast, easy and safe loading and unloading.
Along with its new New Standard HD Punches, large radius punch holder, and radius punches, Wila added a new series of new standard HD dies. All of these dies have 60 degree V-openings to accommodate materials with high levels of springback. Each of these dies is available with optional E2M roller bearings (patent pending) in the bottom of the tang to make them easy to load and unload when used with Wila’s New Standard HD Crowning Systems and lower tool holders with the optional hydraulic lifting feature.
Like all Wila Tooling, all these are CNC-deep hardened on the working surfaces to provide maximum life and long-term accuracy retention.
New standard HD clamping system
The Wila New Standard HD Clamping System is designed to be bolted to the ram of the press brake using Wila’s UPB (Universal Press Brake) mounting system. It's considerably wider than traditional clamping systems. This displaces the pressure over a larger load bearing surface, enabling them to handle tonnage levels up to 84 tons per foot (250 tons per meter) on head loaded new standard punches, and a whopping 269 tons per foot (800 tons per meter) on shoulder loaded new standard punches. They come with CNC-deep hardened working surfaces.
Other key features include hydraulic clamping of punch segments that are 1.575 in. long or longer weighing up to a maximum of 700 lbs.s per foot. They also include an aluminum cover strip with a vernier scale for fast tool location, and a fine adjustment along the Tx axis to provide precision adjustment of the tooling centerline. And finally, they include a guard with a safety mechanism on the end to prevent punches with the E2M Easy To Move roller bearings from being accidently pushed out the end. When used with the Press Brake Productivity ToolStation, the moveable load and unload arm of the tool station will lock and unlock the safety mechanism during tool loading and unloading.
New standard HD crowning systems
Press brakes that are eight feet in length and longer almost always experience some degree of ram and bed deflection when bending longer parts and those that are made of thick materials.
The reason is that while most parts are bent in the center of the machine, the most rigid points of a press brake are near the end where the side frames and the cylinders are located. In the past, a wide variety of ram and bed configurations were tested by various press-brake manufacturers in an attempt to overcome this problem.
However, other than doing time consuming and very costly die shimming, crowning systems are the only solutions that have proven to be effective at neutralizing the problems with ram and bed deflection.
With its New Standard HD System, Wila has introduced a new series of crowning systems that, like its New Standard HD Clamping Systems, are designed to handle the extremely high tonnage levels and harsh demanding conditions that are common to bending thick plate materials. They come in widths of 5.906 in. and 9.843 in. The premium versions are provided with CNC-deep hardened working surfaces and are capable of handling tonnage levels up to 269 tons per foot. The pro versions are capable of handling tonnage levels up to 168 tons per foot.
Wila New Standard HD Crowning Systems are available with an unprecedented list of standard and optional features. Standard features include centralized adjustment of the crown, Wila’s UPB mounting system for direct mounting to the bed of the press brake or a tang for press brakes that have a slot in the bed with set screws and an aluminum cover strip with a vernier scale for fast tool location. Units that are 5.906 in. wide include a fine adjustment along the Tx axis to provide precision adjustment of the tooling centerline. They are also available with hydraulic or manual die clamping.
Optional features include a hydraulic lifting system that actually lifts dies up and off of the load bearing surfaces of the crowning system. When used with Wila’s New Standard HD Dies with E2M roller bearings installed, large heavy dies can be moved in and out of the crowning systems with ease. Other optional features include a CNC-motor drive that automatically sets the crown via the machine’s control when using tooling that weighs up to 8,960 lbs. For applications that require tooling that exceeds 8,960 lbs., Wila provides a hydraulic crowning adjustment
New standard HD lower tool holders
Of course, some press brakes come with crowning systems already built into the machine. For these machines, Wila has made available a full range of New Standard HD Lower Tool Holders. Like their New Standard HD Crowning Systems, the premium versions are provided with CNC-deep hardened working surfaces.
Standard features include hydraulic die clamping, Wila’s UPB mounting system for direct mounting to the bed of the press brake or a tang for press brakes that have a slot in the bed with set-screws, and a fine adjustment along the Tx axis to provide precision adjustment of the tooling centerline.
Optional features include the same hydraulic lifting system available with Wila’s New Standard HD Crowning Systems. When used with Wila’s New Standard HD Dies with E2M roller bearings installed, large heavy dies can be moved in and out of the lower tool holders with ease. They are also available with adjustments along the Ty axis and reference dials with vernier scales to provide optimum parallelism between the upper and lower beams of the press brake.
Press brake productivity tool station
While the majority of this article has been based on the innovations, technical qualities, and heavy duty characteristics of Wila’s New Standard HD Tooling, Clamping, Crowning, and Lower Tool Holder Systems, one component really seems to tie it all together, Wila's Press Brake Productivity ToolStation.
The Wila Press Brake Productivity ToolStation sits off one end of the press brake and acts as both a storage rack and a manually operated tool changer. Its unique loading and unloading arm provides perfect alignment between the ToolStation and the clamping system and crowning system or lower tool holder (whichever applies). This makes it possible to move Wila HD Punches and Dies with E2M roller bearings installed between the press brake and the ToolStation quickly, easily, and safely.
The Press Brake Productivity ToolStation can be provided in 40 in. modules that can be connected as required.
As you can see, the Wila New Standard HD System is more than just a series of heavy duty tooling and components. It represents the first totally integrated system of heavy duty tooling, clamping, crowning, and lower tool holder systems, along with a one of a kind ToolStation that fully addresses the needs of today’s fabricator that processes heavy plate materials.