Designs Stack Up Well Against the Competition
Previous Article Next Article
By Geoff Giordano
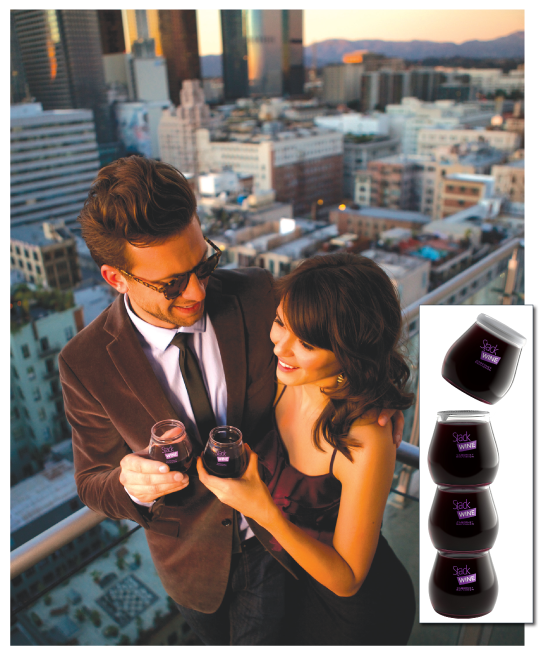
Stack Wines and R&D/Leverage collaborated on a package that delivers a full bottle of wine in four stacked, shatter-proof, individually packaged stemless glasses (inset). The resulting “bottle” of wine is reportedly one-third the weight of a traditional bottle.
In the never-ending quest by brand owners to improve customer satisfaction, lower costs, and protect products during shipping, refining the performance of what holds a product is just as important as the product itself. From coextruded multilayer films to new concepts in blow-molded containers, improved design of packaging—and the molds and tools that produce that packaging—is always breaking new ground.
Quite often, the seeming simplicity of a well-designed package belies the complexity of the tools and processes behind it, notes Michael Paloian, president of Integrated Design Systems in Oyster Bay, New York, USA. At a recent plastics expo, he noted seeing a multicavity mold spitting out bottle caps every second. The mold, he learned, cost roughly $500,000, he recalls—more expensive than the injection molding machine using it.
“The things that are the most interesting are usually the most mundane, especially in disposable packaging,” Paloian asserts. “The things you don’t notice—that you take for granted as a casual observer—are usually the most sophisticated. To get something to a high level of refinement takes a lot of engineering. A case in point would be a bottle cap or a safety cap; designing a safety cap takes a lot of engineering and innovation. To design a beautiful cover with all kinds of contours is not really that complicated.”
Whether enhancing functionality for consumers, using less material, improving processability and recyclability, or shielding sensitive components from harm during shipping, packaging is being taken to new heights.
Consumer Coups Stack Up
For example, some of the winning entries at the 2013 SPE Annual Blow Molding Conference demonstrated advances on a variety of fronts:
- A new PET container for Planters dry roasted peanuts replaces a heavier glass package while still meeting product shelf-life requirements with the use of oxygen barrier technology. According to the award entry form, the Planters PET package uses 84% less packaging by weight, requiring 25% fewer trucks to transport. Produced on a one-step platform of the molding systems maker SIPA, the container retains glass-like clarity while featuring a more ergonomic design with a grip feature.
- New extrusion blow-molded bottles for Crystal Light and Kool-Aid water enhancers feature injection-molded flip-top closures that click twice to tell consumers the container is fully closed. The multilayer bottles feature oxygen and moisture barriers. Heise Industries produced the mold tooling.
- An innovative Pond’s talcum powder container features a one-piece cap allowing one-handed dispensing of the product. By eliminating an inner plug on the cap, the new container reduces 30% of the molds, molding machines, and components previously required; 50% of the assembly time; about 250 tons of polymer; and 200 tons of PVC shrink sleeves, which have been replaced with PET.
“The success of the new package depends upon a new neck design in the bottle,” explains Surendra Agarwal of Creative Group of Industries, which manufactures the package. “The plug is now built into the neck of the bottle. The ultra-precise neck is obtained with IBM technology, [and] all the tooling required to make the inner plug is eliminated.” - Stack Wines and R&D/Leverage collaborated on a package that delivers a full bottle of wine in four shatter-proof, individually packaged stemless glasses. The resulting “bottle” of wine is one-third the weight of a traditional bottle, allowing the consumer to snap apart and even reuse the recyclable glasses.
“The container developed at R&D/Leverage for Stack Wines was unique from the standpoint that a stack feature was required and a snap feature was preferred if possible,” explains Jeff Beason, project engineer for R&D/Leverage.
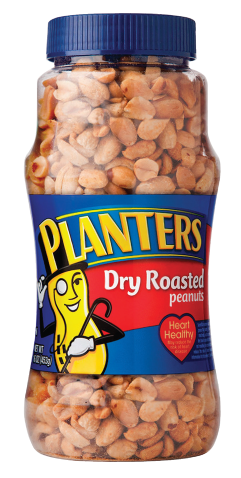
A new PET container for Kraft’s Planters dry roasted peanuts replaces a heavier glass package, while still meeting product shelf-life requirements with the use of oxygen barrier technology (photo courtesy of Kraft).
“The snap feature was the most challenging aspect of the container design and function, but all other features of the container had to be maintained to create a successful product. The mold design had to consider how we would form the features and deal with any difficulties from ejecting the container. The design and process were developed completely in our sample lab with a fully functioning unit tool.”
Matt Zimmer, founder and president of Stack Wines, attests that “creating the snap feature caused a lot of headaches early on. In order for it to function properly, there needed to be an undercut in the base of the bottle. This is really hard to do on traditional equipment, and we had to mesh the right equipment with the right mold designer and the right supplier.” He says the company’s current tool can turn out 24,000 pieces per day.
While Beason can’t divulge exactly how the mold performs, he notes that the project “was developed from concept to reality in a relative short time frame through the unit tool program. Product design, mold design and tooling changes were made in-house during the development phase, and the final design was proved in less than two months. Transferring the mold design to the production platform was seamless, and marketable containers were being produced six months later.”
Development involved several departments including product design, mold design, manufacturing, sample lab, and inspection departments (bottles and tooling). “The production tool was supported in the plant startup by one of our process technicians using the process developed in our lab as a stable beginning,” Beason says. “To start with sketches of an innovative concept and end with a production tool in a short time frame was exciting for both parties. The Stack Wines container’s success ultimately relied on precision tooling and a stable process that was capable of producing consistent features from shot to shot in the multicavity production tool.”
The Stack Wines packaging concept creates a consumer benefit that at one time appeared to elude the spirits sector. Product designer Mark MacLean Blevins recalls an aborted project in a similar vein:
“I did some work a few years ago for a winery in northern California. They wanted to produce a single-serving package shaped like a cup—like an Italian-style jelly glass that families would use to drink their wine at the dinner table. You see these in real Italian restaurants; you’ll see these used instead of stemware. Their first pass at it was an extruded blow molded part so you could get the barrier layer in. But the marketing folks objected to how crude the part was; they wanted something crisp and glass-like, so they wanted injection molding.
“[But] they never could get the product shelf-life and storage life that they needed for a wine product in an injection-molded part. We looked at “after-packaging” packaging—in other words, we would put in this glass and then put six of these glasses in a corrugated container and then put the corrugated container inside a plastic bag filled with nitrogen, pull a vacuum on it [and] heat seal it. But that was far too expensive, far too time consuming, and had far too many fault points to be viable. So it never went [to market]. Now I think there are some processes where we could injection mold that glass and get a barrier in there to allow them to do that.”
According to Henry Vogel, vice president of Heise Industries, “material and resin improvements—along with expanded capabilities in extrusion head technology—have supported the multilayer conversion for shelf-stable packages and the last wave of conversions. The science of blow molding with the barrier to shape and design have tried to expand the window, but it has to be coupled with machine, molds, and resin.
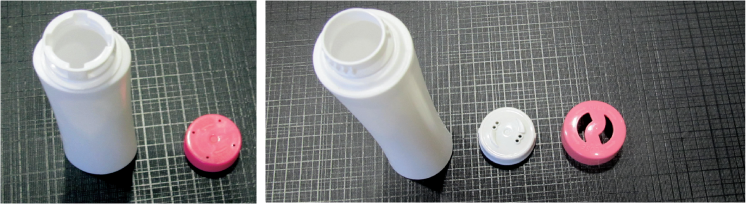
This Pond’s talcum powder container (at left) features a one-piece cap, allowing one-handed dispensing of the product. By eliminating an inner plug on the cap (old design shown at right), the new container reduces 30% of the molds, molding machines, and components previously required. (Photos courtesy of Creative Group of Industries.)
“With the need to lightweight automobiles, airplanes, and more, blow molding and its inherent manufacturing options have seen great challenges and have met them with innovation and resolve. Blow molding has yet to meet every challenge—but it continues to provide a strong economical option for everything from consumer product containers to wind surfers and storage sheds. Everything needs a package, and blow molding is a great solution for many products.”
A Layered Approach
At Nova Chemicals in Moon Township, Pennsylvania, USA, Dan Falla says the buzz about five-layer coextruded films and the “I-beam effect” is growing. Multilayer engineered films for food packaging save costs on premium resins because the core layer is filled with lower-cost materials.
“In the blown film area back in 1990, the predominant films were monolayer,” says Falla, technical service specialist for flexible products. “Over time, you had some five-layer films that came out for barrier applications—but it was very expensive to use that much EVOH (ethylene vinyl alcohol) in the core. Those tended to decline in popularity, while seven- and nine-layer lines became more and more popular for barrier applications. In the meantime, three-layer lines became the predominant blown-film line for polyolefins.
“In about 2008 or 2009, we started to see five-layer lines being promoted for polyolefin applications—and that made a lot of economic sense. You could put lower-cost butenes or hexenes in the skins or employ various other designs to… put all the additives into a very thin, airtight skin.”
What further moved package design toward five-layer film, he says, “was being able to engineer a film structure for specific applications. If you want something that’s really stiff and seals at a low temperature, how do you do that? Through various coextrusion techniques.”
One of those techniques is what he calls the “I-beam effect”: incorporating the high-density PE layers as far apart as possible so they function like an I-beam in building construction. “By separating the high-density layers,” he says, “you can dramatically increase the stiffness of the film without affecting any of other physical properties.”
Increasing film stiffness in this manner allows customers to make their film thinner while still maintaining the speeds necessary for that film to be processed in downstream pieces of equipment such as bagging lines, wicketing lines, or flow wrappers.
Already used in cereal liners and poultry bags, these films have the potential for heavy-duty shipping applications. “Customers can make a significantly stiffer film without affecting tear properties, moisture-transmission rate, or the secant modulus.” And these films save processing time because “you’ll end up getting more square inches out of your line.”
Five-layer films also lower packaging costs. In one example, Falla notes that downgauging a five-layer poultry bag with LLDPE at its core to 2.75 mil (0.070 mm) can produce a bag costing 6.67 cents per msi (thousand square inches)—vs. the 10.6 cents per msi that a 4.0-mil (0.10-mm) bag made entirely of C8 LLDPE cost in 1990.
However, Nova can only recommend to customers the benefits of five-layer film—not always an easy sell. For example, Falla created a five-layer film with a peelable seal that he was able to downgauge from about 3 mils to 2.75 (0.076 to 0.070 mm). The film, which eliminated a polybutene layer and incorporated the I-beam effect with barrier HDPE, reduced the cost per thousand square inches by 15%—but the cost per pound increased.
Depending on the applications, additives in the thinner outer layers of these films can include UV stabilizers, and oxygen scavengers can go in the inside layer. In terms of recycled content, “you could put more ‘repro’ or post-consumer material into some of these layers and reduce the impact on the final performance properties; essentially you can bury it more effectively… separate it behind a functional barrier.”
One key advantage of packaging with five-layer coextruded film is that all five extruders on the production line are identical “so you have less maintenance cost and less inventory of parts. You have five one-inch extruders, and they pretty well all perform the same: same barrel, same screw. From an overall economics perspective that’s a big advantage—and it’s just a marginal increase in cost for five-layer vs. three.”
Next-Level Molds & Tools
In the past five to ten years, there has been a greater tolerance for molders adding complexity to tools using slides and lifters, notes Michael Paloian of Integrated Design Systems. “Many years ago when I was designing parts, it was taboo to put any type of an undercut in a tool. Today, that’s not so frowned upon because of the labor [it saves]. If you have a part where you can put some undercuts in and eliminate another piece or save a few minutes in assembly time, the return on investment is quite attractive; some people will opt to include that in their budget upfront.”
Such advanced molding and tooling is exemplified by companies like Roehr Tool and MMI Engineered Solutions, says Wayne Hertlein, program manager for Wilbert Plastic Services. Roehr’s products help to create next-level molds with collapsible cores and expandable cavities for everything from cosmetic and medical caps to enclosures that protect pipes during shipping for the oil industry
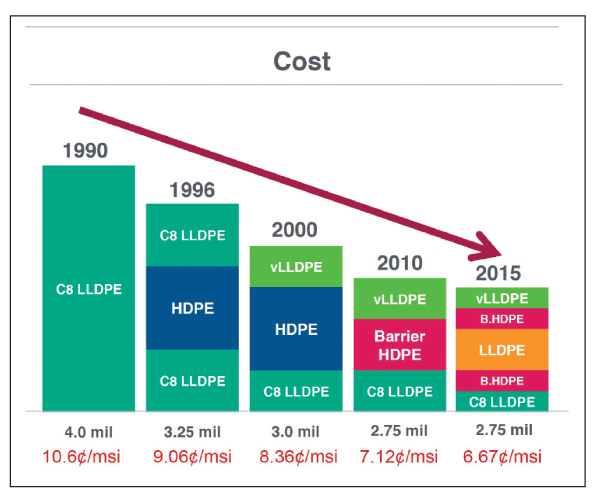
Over the years, the downgauging of film with the use of multiple extruded layers has allowed net cost reductions per thousand square inches (msi) of product (graphic courtesy of Dan Falla of Nova Chemicals).
MMI has standardized a type of tote that can protect sensitive automotive or jet aircraft parts during shipping. Such protective totes prevent damage from static electricity. “The unique thing about that mold is it’s kind of like a Legos set that you can [modify] and have it make a number of different configurations depending on how unique the parts are,” Hertlein explains. These containers can safely package anything, from camshafts or transmission gears to electric modules.
At Roehr, the collapsible core technology introduced by the company’s founder in 1968 has been dramatically refined to create greatly simplified molds that can produce better parts down to 7 mm in diameter and reduce cycle times by 30% on average.
“Our collapsible cores release undercuts on the inside of molded parts, such as threads, which would generally have to be unscrewed from the plastic part in the mold,” explains Roehr general manager Dave Helenius. “We are taking all the complexities of the unscrewing mold—with all its external hardware, including hydraulic cylinders, racks, and gears—and we are putting everything into the core itself… which simplifies the whole mold design.” Also made simpler, he says, are the sequencing of the mold and mold maintenance.
Not only has Roehr produced parts down to 7 mm, it has produced cores in excess of 200 mm in diameter. In between are typical 24-mm caps for pill bottles, all the way up to the industrial-size caps that go on the ends of threaded pipe for the oil-field industry so those pipes are not damaged during transport. Roehr is also working on a project with a 9 3/8-inch (238-mm) diameter, which will be the firm’s largest-diameter core to date.
Roehr traces its current technology back to the collapsible core invented by George Roehr, an MIT graduate. “It was based on a spring-type action,” Helenius explains. “It’s a segmented core body that collapses in on itself under spring-type flexing steel columns.”
In 2006, Progressive Components acquired Roehr Tool, “and in 2007 we started to develop our Dovetail ‘DT’ mechanical collapsible core, in which the collapsing segments are driven on a center pin with dovetails. The cores are shorter [and] more robust and hold up to the harsh injection-molding environment better than the spring-type cores. They are also easier to maintain; our Quick Lock feature allows the cores to be removed from the mold individually for cleaning or maintenance while the mold is still in the press.”
Since releasing the DT collapsible cores at NPE 2009 in Chicago, “we are gaining industry acceptance… and it’s been doing very well for us in both the consumer packaging and industrial markets,” Helenius says.
Meanwhile, the expandable cavity “is a solution for the opposite of internal threads,” Helenius explains. “Expandable cavities create threads or undercuts on the outside of a molded part.” Generally in an injection molding situation, he continues, “you would have side actions forming your undercuts on the outside. You would have side-action slides with gibs, locks, and angle pins to mechanically drive them open. Our expandable cavities are a one-piece unit [and] generally a four-segment design—but we can do any number of segments required.”
In terms of cost, Roehr says its dovetail collapsible core molds are in line with other molds. “We are eliminating the superstructure of an unscrewing mold—the cylinders, the racks, the gears—so you’re saving money there. But our cores are a little more expensive because all the complexities are integral to the core itself.” While their molds with more than 16 cavities might be a bit more expensive, Helenius notes, the return on investment is realized relatively quickly with cycle-time reductions, reduced maintenance costs, and ease of operation.
Thanks to a development breakthrough last year, Helenius says, Roehr introduced its Sub-10 DT core series, which has allowed the company to better serve the medical and electrical connector industries with small parts featuring internal undercuts. And while also serving the automotive and aviation industries, Roehr’s technology is used to produce caps for cosmetics as well.
Ultimately, Helenius says, “our tools turn a really complex mold into something that is pretty basic.”
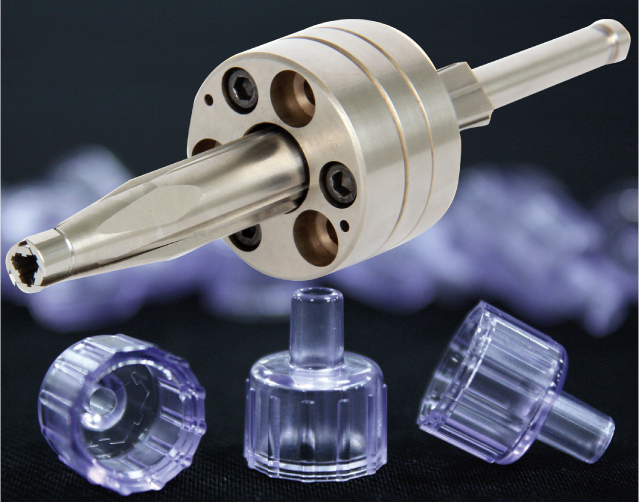
The Sub-10 Dovetail (DT) collapsible core from Roehr Tool Corp. allows the molding of very small threaded caps and closures. DT collapsible cores simplify mold design, build, and maintenance, plus they reportedly can reduce cycle times by up to 30% on average. (Photo courtesy of Roehr Tool.)
Designs Stack Up Well Against the Competition
Previous Article Next Article
By Geoff Giordano
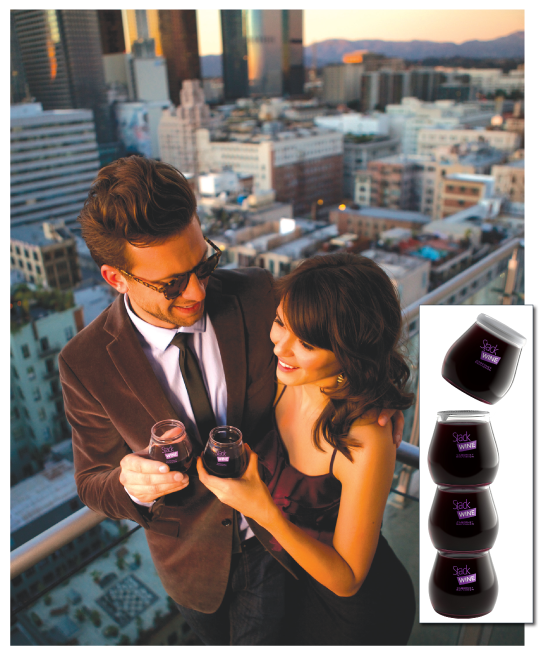
Stack Wines and R&D/Leverage collaborated on a package that delivers a full bottle of wine in four stacked, shatter-proof, individually packaged stemless glasses (inset). The resulting “bottle” of wine is reportedly one-third the weight of a traditional bottle.
In the never-ending quest by brand owners to improve customer satisfaction, lower costs, and protect products during shipping, refining the performance of what holds a product is just as important as the product itself. From coextruded multilayer films to new concepts in blow-molded containers, improved design of packaging—and the molds and tools that produce that packaging—is always breaking new ground.
Quite often, the seeming simplicity of a well-designed package belies the complexity of the tools and processes behind it, notes Michael Paloian, president of Integrated Design Systems in Oyster Bay, New York, USA. At a recent plastics expo, he noted seeing a multicavity mold spitting out bottle caps every second. The mold, he learned, cost roughly $500,000, he recalls—more expensive than the injection molding machine using it.
“The things that are the most interesting are usually the most mundane, especially in disposable packaging,” Paloian asserts. “The things you don’t notice—that you take for granted as a casual observer—are usually the most sophisticated. To get something to a high level of refinement takes a lot of engineering. A case in point would be a bottle cap or a safety cap; designing a safety cap takes a lot of engineering and innovation. To design a beautiful cover with all kinds of contours is not really that complicated.”
Whether enhancing functionality for consumers, using less material, improving processability and recyclability, or shielding sensitive components from harm during shipping, packaging is being taken to new heights.
Consumer Coups Stack Up
For example, some of the winning entries at the 2013 SPE Annual Blow Molding Conference demonstrated advances on a variety of fronts:
- A new PET container for Planters dry roasted peanuts replaces a heavier glass package while still meeting product shelf-life requirements with the use of oxygen barrier technology. According to the award entry form, the Planters PET package uses 84% less packaging by weight, requiring 25% fewer trucks to transport. Produced on a one-step platform of the molding systems maker SIPA, the container retains glass-like clarity while featuring a more ergonomic design with a grip feature.
- New extrusion blow-molded bottles for Crystal Light and Kool-Aid water enhancers feature injection-molded flip-top closures that click twice to tell consumers the container is fully closed. The multilayer bottles feature oxygen and moisture barriers. Heise Industries produced the mold tooling.
- An innovative Pond’s talcum powder container features a one-piece cap allowing one-handed dispensing of the product. By eliminating an inner plug on the cap, the new container reduces 30% of the molds, molding machines, and components previously required; 50% of the assembly time; about 250 tons of polymer; and 200 tons of PVC shrink sleeves, which have been replaced with PET.
“The success of the new package depends upon a new neck design in the bottle,” explains Surendra Agarwal of Creative Group of Industries, which manufactures the package. “The plug is now built into the neck of the bottle. The ultra-precise neck is obtained with IBM technology, [and] all the tooling required to make the inner plug is eliminated.” - Stack Wines and R&D/Leverage collaborated on a package that delivers a full bottle of wine in four shatter-proof, individually packaged stemless glasses. The resulting “bottle” of wine is one-third the weight of a traditional bottle, allowing the consumer to snap apart and even reuse the recyclable glasses.
“The container developed at R&D/Leverage for Stack Wines was unique from the standpoint that a stack feature was required and a snap feature was preferred if possible,” explains Jeff Beason, project engineer for R&D/Leverage.
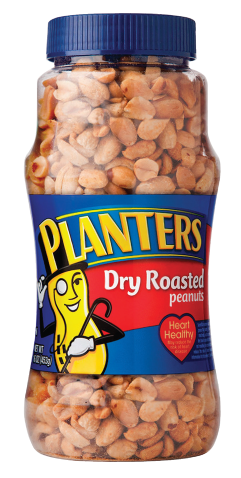
A new PET container for Kraft’s Planters dry roasted peanuts replaces a heavier glass package, while still meeting product shelf-life requirements with the use of oxygen barrier technology (photo courtesy of Kraft).
“The snap feature was the most challenging aspect of the container design and function, but all other features of the container had to be maintained to create a successful product. The mold design had to consider how we would form the features and deal with any difficulties from ejecting the container. The design and process were developed completely in our sample lab with a fully functioning unit tool.”
Matt Zimmer, founder and president of Stack Wines, attests that “creating the snap feature caused a lot of headaches early on. In order for it to function properly, there needed to be an undercut in the base of the bottle. This is really hard to do on traditional equipment, and we had to mesh the right equipment with the right mold designer and the right supplier.” He says the company’s current tool can turn out 24,000 pieces per day.
While Beason can’t divulge exactly how the mold performs, he notes that the project “was developed from concept to reality in a relative short time frame through the unit tool program. Product design, mold design and tooling changes were made in-house during the development phase, and the final design was proved in less than two months. Transferring the mold design to the production platform was seamless, and marketable containers were being produced six months later.”
Development involved several departments including product design, mold design, manufacturing, sample lab, and inspection departments (bottles and tooling). “The production tool was supported in the plant startup by one of our process technicians using the process developed in our lab as a stable beginning,” Beason says. “To start with sketches of an innovative concept and end with a production tool in a short time frame was exciting for both parties. The Stack Wines container’s success ultimately relied on precision tooling and a stable process that was capable of producing consistent features from shot to shot in the multicavity production tool.”
The Stack Wines packaging concept creates a consumer benefit that at one time appeared to elude the spirits sector. Product designer Mark MacLean Blevins recalls an aborted project in a similar vein:
“I did some work a few years ago for a winery in northern California. They wanted to produce a single-serving package shaped like a cup—like an Italian-style jelly glass that families would use to drink their wine at the dinner table. You see these in real Italian restaurants; you’ll see these used instead of stemware. Their first pass at it was an extruded blow molded part so you could get the barrier layer in. But the marketing folks objected to how crude the part was; they wanted something crisp and glass-like, so they wanted injection molding.
“[But] they never could get the product shelf-life and storage life that they needed for a wine product in an injection-molded part. We looked at “after-packaging” packaging—in other words, we would put in this glass and then put six of these glasses in a corrugated container and then put the corrugated container inside a plastic bag filled with nitrogen, pull a vacuum on it [and] heat seal it. But that was far too expensive, far too time consuming, and had far too many fault points to be viable. So it never went [to market]. Now I think there are some processes where we could injection mold that glass and get a barrier in there to allow them to do that.”
According to Henry Vogel, vice president of Heise Industries, “material and resin improvements—along with expanded capabilities in extrusion head technology—have supported the multilayer conversion for shelf-stable packages and the last wave of conversions. The science of blow molding with the barrier to shape and design have tried to expand the window, but it has to be coupled with machine, molds, and resin.
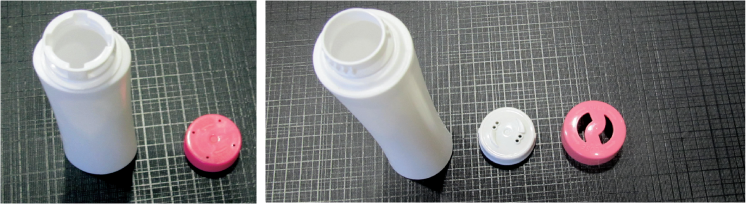
This Pond’s talcum powder container (at left) features a one-piece cap, allowing one-handed dispensing of the product. By eliminating an inner plug on the cap (old design shown at right), the new container reduces 30% of the molds, molding machines, and components previously required. (Photos courtesy of Creative Group of Industries.)
“With the need to lightweight automobiles, airplanes, and more, blow molding and its inherent manufacturing options have seen great challenges and have met them with innovation and resolve. Blow molding has yet to meet every challenge—but it continues to provide a strong economical option for everything from consumer product containers to wind surfers and storage sheds. Everything needs a package, and blow molding is a great solution for many products.”
A Layered Approach
At Nova Chemicals in Moon Township, Pennsylvania, USA, Dan Falla says the buzz about five-layer coextruded films and the “I-beam effect” is growing. Multilayer engineered films for food packaging save costs on premium resins because the core layer is filled with lower-cost materials.
“In the blown film area back in 1990, the predominant films were monolayer,” says Falla, technical service specialist for flexible products. “Over time, you had some five-layer films that came out for barrier applications—but it was very expensive to use that much EVOH (ethylene vinyl alcohol) in the core. Those tended to decline in popularity, while seven- and nine-layer lines became more and more popular for barrier applications. In the meantime, three-layer lines became the predominant blown-film line for polyolefins.
“In about 2008 or 2009, we started to see five-layer lines being promoted for polyolefin applications—and that made a lot of economic sense. You could put lower-cost butenes or hexenes in the skins or employ various other designs to… put all the additives into a very thin, airtight skin.”
What further moved package design toward five-layer film, he says, “was being able to engineer a film structure for specific applications. If you want something that’s really stiff and seals at a low temperature, how do you do that? Through various coextrusion techniques.”
One of those techniques is what he calls the “I-beam effect”: incorporating the high-density PE layers as far apart as possible so they function like an I-beam in building construction. “By separating the high-density layers,” he says, “you can dramatically increase the stiffness of the film without affecting any of other physical properties.”
Increasing film stiffness in this manner allows customers to make their film thinner while still maintaining the speeds necessary for that film to be processed in downstream pieces of equipment such as bagging lines, wicketing lines, or flow wrappers.
Already used in cereal liners and poultry bags, these films have the potential for heavy-duty shipping applications. “Customers can make a significantly stiffer film without affecting tear properties, moisture-transmission rate, or the secant modulus.” And these films save processing time because “you’ll end up getting more square inches out of your line.”
Five-layer films also lower packaging costs. In one example, Falla notes that downgauging a five-layer poultry bag with LLDPE at its core to 2.75 mil (0.070 mm) can produce a bag costing 6.67 cents per msi (thousand square inches)—vs. the 10.6 cents per msi that a 4.0-mil (0.10-mm) bag made entirely of C8 LLDPE cost in 1990.
However, Nova can only recommend to customers the benefits of five-layer film—not always an easy sell. For example, Falla created a five-layer film with a peelable seal that he was able to downgauge from about 3 mils to 2.75 (0.076 to 0.070 mm). The film, which eliminated a polybutene layer and incorporated the I-beam effect with barrier HDPE, reduced the cost per thousand square inches by 15%—but the cost per pound increased.
Depending on the applications, additives in the thinner outer layers of these films can include UV stabilizers, and oxygen scavengers can go in the inside layer. In terms of recycled content, “you could put more ‘repro’ or post-consumer material into some of these layers and reduce the impact on the final performance properties; essentially you can bury it more effectively… separate it behind a functional barrier.”
One key advantage of packaging with five-layer coextruded film is that all five extruders on the production line are identical “so you have less maintenance cost and less inventory of parts. You have five one-inch extruders, and they pretty well all perform the same: same barrel, same screw. From an overall economics perspective that’s a big advantage—and it’s just a marginal increase in cost for five-layer vs. three.”
Next-Level Molds & Tools
In the past five to ten years, there has been a greater tolerance for molders adding complexity to tools using slides and lifters, notes Michael Paloian of Integrated Design Systems. “Many years ago when I was designing parts, it was taboo to put any type of an undercut in a tool. Today, that’s not so frowned upon because of the labor [it saves]. If you have a part where you can put some undercuts in and eliminate another piece or save a few minutes in assembly time, the return on investment is quite attractive; some people will opt to include that in their budget upfront.”
Such advanced molding and tooling is exemplified by companies like Roehr Tool and MMI Engineered Solutions, says Wayne Hertlein, program manager for Wilbert Plastic Services. Roehr’s products help to create next-level molds with collapsible cores and expandable cavities for everything from cosmetic and medical caps to enclosures that protect pipes during shipping for the oil industry
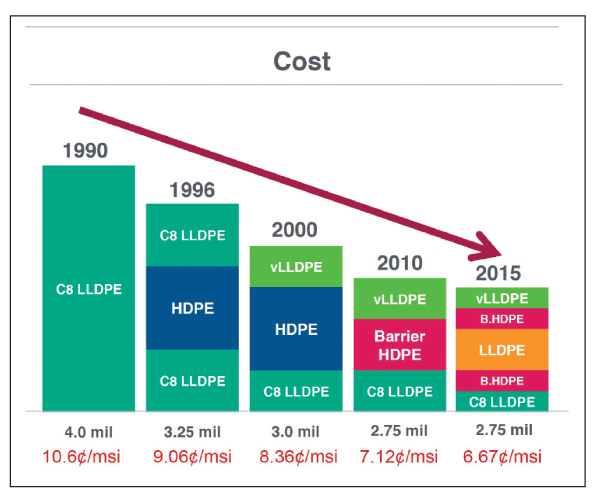
Over the years, the downgauging of film with the use of multiple extruded layers has allowed net cost reductions per thousand square inches (msi) of product (graphic courtesy of Dan Falla of Nova Chemicals).
MMI has standardized a type of tote that can protect sensitive automotive or jet aircraft parts during shipping. Such protective totes prevent damage from static electricity. “The unique thing about that mold is it’s kind of like a Legos set that you can [modify] and have it make a number of different configurations depending on how unique the parts are,” Hertlein explains. These containers can safely package anything, from camshafts or transmission gears to electric modules.
At Roehr, the collapsible core technology introduced by the company’s founder in 1968 has been dramatically refined to create greatly simplified molds that can produce better parts down to 7 mm in diameter and reduce cycle times by 30% on average.
“Our collapsible cores release undercuts on the inside of molded parts, such as threads, which would generally have to be unscrewed from the plastic part in the mold,” explains Roehr general manager Dave Helenius. “We are taking all the complexities of the unscrewing mold—with all its external hardware, including hydraulic cylinders, racks, and gears—and we are putting everything into the core itself… which simplifies the whole mold design.” Also made simpler, he says, are the sequencing of the mold and mold maintenance.
Not only has Roehr produced parts down to 7 mm, it has produced cores in excess of 200 mm in diameter. In between are typical 24-mm caps for pill bottles, all the way up to the industrial-size caps that go on the ends of threaded pipe for the oil-field industry so those pipes are not damaged during transport. Roehr is also working on a project with a 9 3/8-inch (238-mm) diameter, which will be the firm’s largest-diameter core to date.
Roehr traces its current technology back to the collapsible core invented by George Roehr, an MIT graduate. “It was based on a spring-type action,” Helenius explains. “It’s a segmented core body that collapses in on itself under spring-type flexing steel columns.”
In 2006, Progressive Components acquired Roehr Tool, “and in 2007 we started to develop our Dovetail ‘DT’ mechanical collapsible core, in which the collapsing segments are driven on a center pin with dovetails. The cores are shorter [and] more robust and hold up to the harsh injection-molding environment better than the spring-type cores. They are also easier to maintain; our Quick Lock feature allows the cores to be removed from the mold individually for cleaning or maintenance while the mold is still in the press.”
Since releasing the DT collapsible cores at NPE 2009 in Chicago, “we are gaining industry acceptance… and it’s been doing very well for us in both the consumer packaging and industrial markets,” Helenius says.
Meanwhile, the expandable cavity “is a solution for the opposite of internal threads,” Helenius explains. “Expandable cavities create threads or undercuts on the outside of a molded part.” Generally in an injection molding situation, he continues, “you would have side actions forming your undercuts on the outside. You would have side-action slides with gibs, locks, and angle pins to mechanically drive them open. Our expandable cavities are a one-piece unit [and] generally a four-segment design—but we can do any number of segments required.”
In terms of cost, Roehr says its dovetail collapsible core molds are in line with other molds. “We are eliminating the superstructure of an unscrewing mold—the cylinders, the racks, the gears—so you’re saving money there. But our cores are a little more expensive because all the complexities are integral to the core itself.” While their molds with more than 16 cavities might be a bit more expensive, Helenius notes, the return on investment is realized relatively quickly with cycle-time reductions, reduced maintenance costs, and ease of operation.
Thanks to a development breakthrough last year, Helenius says, Roehr introduced its Sub-10 DT core series, which has allowed the company to better serve the medical and electrical connector industries with small parts featuring internal undercuts. And while also serving the automotive and aviation industries, Roehr’s technology is used to produce caps for cosmetics as well.
Ultimately, Helenius says, “our tools turn a really complex mold into something that is pretty basic.”
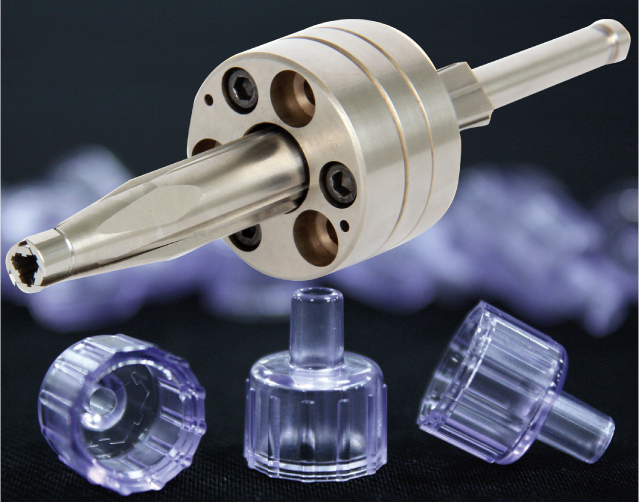
The Sub-10 Dovetail (DT) collapsible core from Roehr Tool Corp. allows the molding of very small threaded caps and closures. DT collapsible cores simplify mold design, build, and maintenance, plus they reportedly can reduce cycle times by up to 30% on average. (Photo courtesy of Roehr Tool.)
Designs Stack Up Well Against the Competition
Previous Article Next Article
By Geoff Giordano
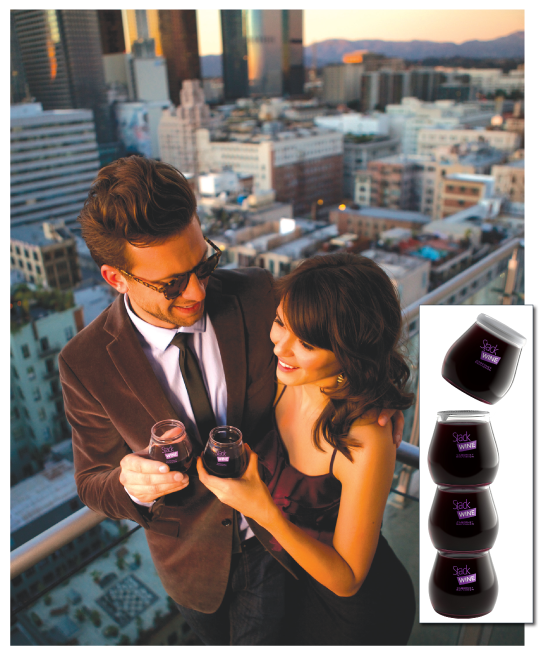
Stack Wines and R&D/Leverage collaborated on a package that delivers a full bottle of wine in four stacked, shatter-proof, individually packaged stemless glasses (inset). The resulting “bottle” of wine is reportedly one-third the weight of a traditional bottle.
In the never-ending quest by brand owners to improve customer satisfaction, lower costs, and protect products during shipping, refining the performance of what holds a product is just as important as the product itself. From coextruded multilayer films to new concepts in blow-molded containers, improved design of packaging—and the molds and tools that produce that packaging—is always breaking new ground.
Quite often, the seeming simplicity of a well-designed package belies the complexity of the tools and processes behind it, notes Michael Paloian, president of Integrated Design Systems in Oyster Bay, New York, USA. At a recent plastics expo, he noted seeing a multicavity mold spitting out bottle caps every second. The mold, he learned, cost roughly $500,000, he recalls—more expensive than the injection molding machine using it.
“The things that are the most interesting are usually the most mundane, especially in disposable packaging,” Paloian asserts. “The things you don’t notice—that you take for granted as a casual observer—are usually the most sophisticated. To get something to a high level of refinement takes a lot of engineering. A case in point would be a bottle cap or a safety cap; designing a safety cap takes a lot of engineering and innovation. To design a beautiful cover with all kinds of contours is not really that complicated.”
Whether enhancing functionality for consumers, using less material, improving processability and recyclability, or shielding sensitive components from harm during shipping, packaging is being taken to new heights.
Consumer Coups Stack Up
For example, some of the winning entries at the 2013 SPE Annual Blow Molding Conference demonstrated advances on a variety of fronts:
- A new PET container for Planters dry roasted peanuts replaces a heavier glass package while still meeting product shelf-life requirements with the use of oxygen barrier technology. According to the award entry form, the Planters PET package uses 84% less packaging by weight, requiring 25% fewer trucks to transport. Produced on a one-step platform of the molding systems maker SIPA, the container retains glass-like clarity while featuring a more ergonomic design with a grip feature.
- New extrusion blow-molded bottles for Crystal Light and Kool-Aid water enhancers feature injection-molded flip-top closures that click twice to tell consumers the container is fully closed. The multilayer bottles feature oxygen and moisture barriers. Heise Industries produced the mold tooling.
- An innovative Pond’s talcum powder container features a one-piece cap allowing one-handed dispensing of the product. By eliminating an inner plug on the cap, the new container reduces 30% of the molds, molding machines, and components previously required; 50% of the assembly time; about 250 tons of polymer; and 200 tons of PVC shrink sleeves, which have been replaced with PET.
“The success of the new package depends upon a new neck design in the bottle,” explains Surendra Agarwal of Creative Group of Industries, which manufactures the package. “The plug is now built into the neck of the bottle. The ultra-precise neck is obtained with IBM technology, [and] all the tooling required to make the inner plug is eliminated.” - Stack Wines and R&D/Leverage collaborated on a package that delivers a full bottle of wine in four shatter-proof, individually packaged stemless glasses. The resulting “bottle” of wine is one-third the weight of a traditional bottle, allowing the consumer to snap apart and even reuse the recyclable glasses.
“The container developed at R&D/Leverage for Stack Wines was unique from the standpoint that a stack feature was required and a snap feature was preferred if possible,” explains Jeff Beason, project engineer for R&D/Leverage.
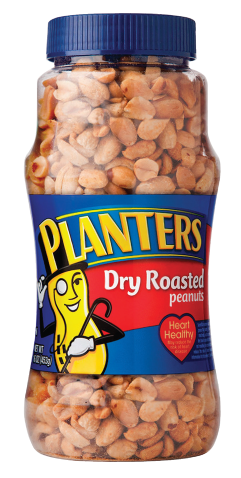
A new PET container for Kraft’s Planters dry roasted peanuts replaces a heavier glass package, while still meeting product shelf-life requirements with the use of oxygen barrier technology (photo courtesy of Kraft).
“The snap feature was the most challenging aspect of the container design and function, but all other features of the container had to be maintained to create a successful product. The mold design had to consider how we would form the features and deal with any difficulties from ejecting the container. The design and process were developed completely in our sample lab with a fully functioning unit tool.”
Matt Zimmer, founder and president of Stack Wines, attests that “creating the snap feature caused a lot of headaches early on. In order for it to function properly, there needed to be an undercut in the base of the bottle. This is really hard to do on traditional equipment, and we had to mesh the right equipment with the right mold designer and the right supplier.” He says the company’s current tool can turn out 24,000 pieces per day.
While Beason can’t divulge exactly how the mold performs, he notes that the project “was developed from concept to reality in a relative short time frame through the unit tool program. Product design, mold design and tooling changes were made in-house during the development phase, and the final design was proved in less than two months. Transferring the mold design to the production platform was seamless, and marketable containers were being produced six months later.”
Development involved several departments including product design, mold design, manufacturing, sample lab, and inspection departments (bottles and tooling). “The production tool was supported in the plant startup by one of our process technicians using the process developed in our lab as a stable beginning,” Beason says. “To start with sketches of an innovative concept and end with a production tool in a short time frame was exciting for both parties. The Stack Wines container’s success ultimately relied on precision tooling and a stable process that was capable of producing consistent features from shot to shot in the multicavity production tool.”
The Stack Wines packaging concept creates a consumer benefit that at one time appeared to elude the spirits sector. Product designer Mark MacLean Blevins recalls an aborted project in a similar vein:
“I did some work a few years ago for a winery in northern California. They wanted to produce a single-serving package shaped like a cup—like an Italian-style jelly glass that families would use to drink their wine at the dinner table. You see these in real Italian restaurants; you’ll see these used instead of stemware. Their first pass at it was an extruded blow molded part so you could get the barrier layer in. But the marketing folks objected to how crude the part was; they wanted something crisp and glass-like, so they wanted injection molding.
“[But] they never could get the product shelf-life and storage life that they needed for a wine product in an injection-molded part. We looked at “after-packaging” packaging—in other words, we would put in this glass and then put six of these glasses in a corrugated container and then put the corrugated container inside a plastic bag filled with nitrogen, pull a vacuum on it [and] heat seal it. But that was far too expensive, far too time consuming, and had far too many fault points to be viable. So it never went [to market]. Now I think there are some processes where we could injection mold that glass and get a barrier in there to allow them to do that.”
According to Henry Vogel, vice president of Heise Industries, “material and resin improvements—along with expanded capabilities in extrusion head technology—have supported the multilayer conversion for shelf-stable packages and the last wave of conversions. The science of blow molding with the barrier to shape and design have tried to expand the window, but it has to be coupled with machine, molds, and resin.
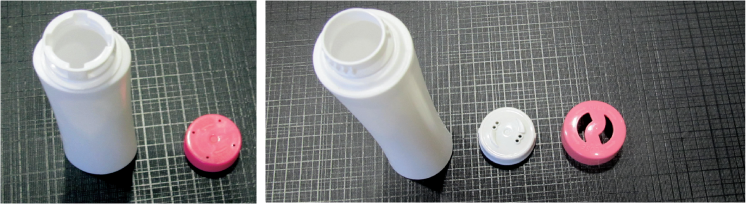
This Pond’s talcum powder container (at left) features a one-piece cap, allowing one-handed dispensing of the product. By eliminating an inner plug on the cap (old design shown at right), the new container reduces 30% of the molds, molding machines, and components previously required. (Photos courtesy of Creative Group of Industries.)
“With the need to lightweight automobiles, airplanes, and more, blow molding and its inherent manufacturing options have seen great challenges and have met them with innovation and resolve. Blow molding has yet to meet every challenge—but it continues to provide a strong economical option for everything from consumer product containers to wind surfers and storage sheds. Everything needs a package, and blow molding is a great solution for many products.”
A Layered Approach
At Nova Chemicals in Moon Township, Pennsylvania, USA, Dan Falla says the buzz about five-layer coextruded films and the “I-beam effect” is growing. Multilayer engineered films for food packaging save costs on premium resins because the core layer is filled with lower-cost materials.
“In the blown film area back in 1990, the predominant films were monolayer,” says Falla, technical service specialist for flexible products. “Over time, you had some five-layer films that came out for barrier applications—but it was very expensive to use that much EVOH (ethylene vinyl alcohol) in the core. Those tended to decline in popularity, while seven- and nine-layer lines became more and more popular for barrier applications. In the meantime, three-layer lines became the predominant blown-film line for polyolefins.
“In about 2008 or 2009, we started to see five-layer lines being promoted for polyolefin applications—and that made a lot of economic sense. You could put lower-cost butenes or hexenes in the skins or employ various other designs to… put all the additives into a very thin, airtight skin.”
What further moved package design toward five-layer film, he says, “was being able to engineer a film structure for specific applications. If you want something that’s really stiff and seals at a low temperature, how do you do that? Through various coextrusion techniques.”
One of those techniques is what he calls the “I-beam effect”: incorporating the high-density PE layers as far apart as possible so they function like an I-beam in building construction. “By separating the high-density layers,” he says, “you can dramatically increase the stiffness of the film without affecting any of other physical properties.”
Increasing film stiffness in this manner allows customers to make their film thinner while still maintaining the speeds necessary for that film to be processed in downstream pieces of equipment such as bagging lines, wicketing lines, or flow wrappers.
Already used in cereal liners and poultry bags, these films have the potential for heavy-duty shipping applications. “Customers can make a significantly stiffer film without affecting tear properties, moisture-transmission rate, or the secant modulus.” And these films save processing time because “you’ll end up getting more square inches out of your line.”
Five-layer films also lower packaging costs. In one example, Falla notes that downgauging a five-layer poultry bag with LLDPE at its core to 2.75 mil (0.070 mm) can produce a bag costing 6.67 cents per msi (thousand square inches)—vs. the 10.6 cents per msi that a 4.0-mil (0.10-mm) bag made entirely of C8 LLDPE cost in 1990.
However, Nova can only recommend to customers the benefits of five-layer film—not always an easy sell. For example, Falla created a five-layer film with a peelable seal that he was able to downgauge from about 3 mils to 2.75 (0.076 to 0.070 mm). The film, which eliminated a polybutene layer and incorporated the I-beam effect with barrier HDPE, reduced the cost per thousand square inches by 15%—but the cost per pound increased.
Depending on the applications, additives in the thinner outer layers of these films can include UV stabilizers, and oxygen scavengers can go in the inside layer. In terms of recycled content, “you could put more ‘repro’ or post-consumer material into some of these layers and reduce the impact on the final performance properties; essentially you can bury it more effectively… separate it behind a functional barrier.”
One key advantage of packaging with five-layer coextruded film is that all five extruders on the production line are identical “so you have less maintenance cost and less inventory of parts. You have five one-inch extruders, and they pretty well all perform the same: same barrel, same screw. From an overall economics perspective that’s a big advantage—and it’s just a marginal increase in cost for five-layer vs. three.”
Next-Level Molds & Tools
In the past five to ten years, there has been a greater tolerance for molders adding complexity to tools using slides and lifters, notes Michael Paloian of Integrated Design Systems. “Many years ago when I was designing parts, it was taboo to put any type of an undercut in a tool. Today, that’s not so frowned upon because of the labor [it saves]. If you have a part where you can put some undercuts in and eliminate another piece or save a few minutes in assembly time, the return on investment is quite attractive; some people will opt to include that in their budget upfront.”
Such advanced molding and tooling is exemplified by companies like Roehr Tool and MMI Engineered Solutions, says Wayne Hertlein, program manager for Wilbert Plastic Services. Roehr’s products help to create next-level molds with collapsible cores and expandable cavities for everything from cosmetic and medical caps to enclosures that protect pipes during shipping for the oil industry
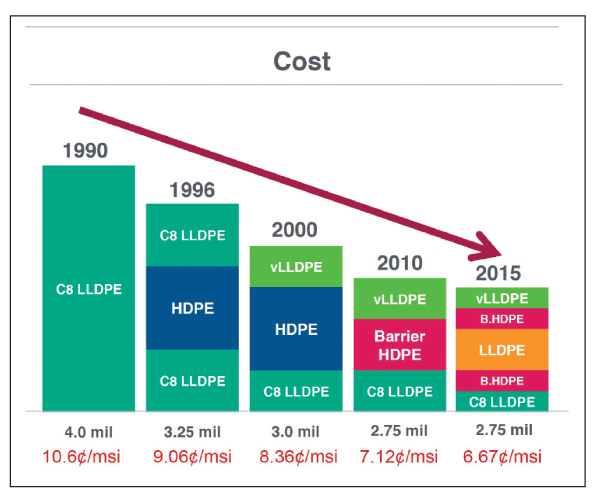
Over the years, the downgauging of film with the use of multiple extruded layers has allowed net cost reductions per thousand square inches (msi) of product (graphic courtesy of Dan Falla of Nova Chemicals).
MMI has standardized a type of tote that can protect sensitive automotive or jet aircraft parts during shipping. Such protective totes prevent damage from static electricity. “The unique thing about that mold is it’s kind of like a Legos set that you can [modify] and have it make a number of different configurations depending on how unique the parts are,” Hertlein explains. These containers can safely package anything, from camshafts or transmission gears to electric modules.
At Roehr, the collapsible core technology introduced by the company’s founder in 1968 has been dramatically refined to create greatly simplified molds that can produce better parts down to 7 mm in diameter and reduce cycle times by 30% on average.
“Our collapsible cores release undercuts on the inside of molded parts, such as threads, which would generally have to be unscrewed from the plastic part in the mold,” explains Roehr general manager Dave Helenius. “We are taking all the complexities of the unscrewing mold—with all its external hardware, including hydraulic cylinders, racks, and gears—and we are putting everything into the core itself… which simplifies the whole mold design.” Also made simpler, he says, are the sequencing of the mold and mold maintenance.
Not only has Roehr produced parts down to 7 mm, it has produced cores in excess of 200 mm in diameter. In between are typical 24-mm caps for pill bottles, all the way up to the industrial-size caps that go on the ends of threaded pipe for the oil-field industry so those pipes are not damaged during transport. Roehr is also working on a project with a 9 3/8-inch (238-mm) diameter, which will be the firm’s largest-diameter core to date.
Roehr traces its current technology back to the collapsible core invented by George Roehr, an MIT graduate. “It was based on a spring-type action,” Helenius explains. “It’s a segmented core body that collapses in on itself under spring-type flexing steel columns.”
In 2006, Progressive Components acquired Roehr Tool, “and in 2007 we started to develop our Dovetail ‘DT’ mechanical collapsible core, in which the collapsing segments are driven on a center pin with dovetails. The cores are shorter [and] more robust and hold up to the harsh injection-molding environment better than the spring-type cores. They are also easier to maintain; our Quick Lock feature allows the cores to be removed from the mold individually for cleaning or maintenance while the mold is still in the press.”
Since releasing the DT collapsible cores at NPE 2009 in Chicago, “we are gaining industry acceptance… and it’s been doing very well for us in both the consumer packaging and industrial markets,” Helenius says.
Meanwhile, the expandable cavity “is a solution for the opposite of internal threads,” Helenius explains. “Expandable cavities create threads or undercuts on the outside of a molded part.” Generally in an injection molding situation, he continues, “you would have side actions forming your undercuts on the outside. You would have side-action slides with gibs, locks, and angle pins to mechanically drive them open. Our expandable cavities are a one-piece unit [and] generally a four-segment design—but we can do any number of segments required.”
In terms of cost, Roehr says its dovetail collapsible core molds are in line with other molds. “We are eliminating the superstructure of an unscrewing mold—the cylinders, the racks, the gears—so you’re saving money there. But our cores are a little more expensive because all the complexities are integral to the core itself.” While their molds with more than 16 cavities might be a bit more expensive, Helenius notes, the return on investment is realized relatively quickly with cycle-time reductions, reduced maintenance costs, and ease of operation.
Thanks to a development breakthrough last year, Helenius says, Roehr introduced its Sub-10 DT core series, which has allowed the company to better serve the medical and electrical connector industries with small parts featuring internal undercuts. And while also serving the automotive and aviation industries, Roehr’s technology is used to produce caps for cosmetics as well.
Ultimately, Helenius says, “our tools turn a really complex mold into something that is pretty basic.”
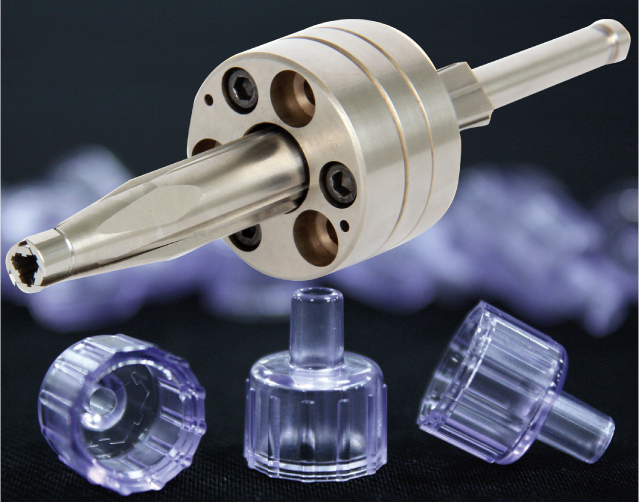
The Sub-10 Dovetail (DT) collapsible core from Roehr Tool Corp. allows the molding of very small threaded caps and closures. DT collapsible cores simplify mold design, build, and maintenance, plus they reportedly can reduce cycle times by up to 30% on average. (Photo courtesy of Roehr Tool.)