NPE in 3-D
Previous Article Next Article
By Geoff Giordano
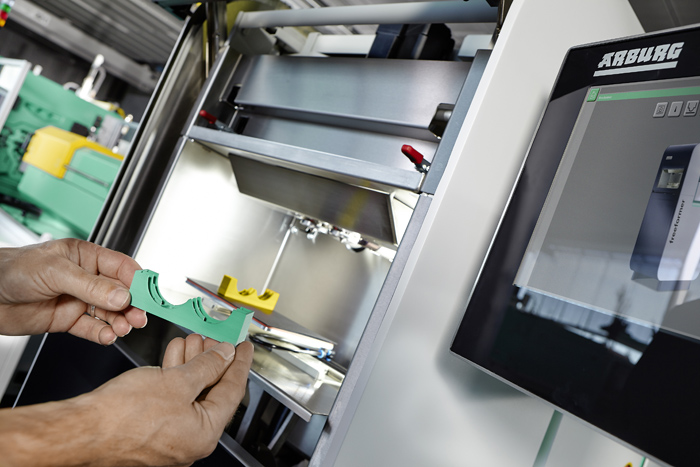
Arburg’s Freeformer 3-D-prints functional parts in thermoplastic resins. Because it works with molten plastic, it produces no dust or emissions, and it can be used to mass-produce items with customization, like three-dimensional lettering. (Photo courtesy of Arburg.)
When manufacturing equipment maker Arburg decided to become a sponsor of the first-ever NPE3D pavilion at NPE2015 in Orlando in March, it was an obvious win-win situation.
“We celebrated the premiere of our Freeformer at K [Show] 2013,” says Heinz Gaub, managing director of Technology & Engineering for Arburg (and an ANTEC® Orlando 2015 plenary speaker). “In 2014, the first development customers in Germany received delivery of this system for industrial additive manufacturing. The next phase in the region-by-region introduction will see the product launch in the European and overseas markets in spring 2015.
“We deliberately decided to schedule the Freeformer’s sales launch in America to coincide with the NPE show. NPE3D offers us the perfect platform for making contact with plastics processors from outside the injection molding sector in the U.S.”
With the 3-D printing revolution in full swing, NPE2015 has created a dedicated exhibit area featuring nearly 20 companies representing many facets of additive manufacturing. In addition, SPI has scheduled six 3-D printing presentations on Tuesday, March 24, during its Business of Plastics Conference.
Demand for the NPE3D pavilion was so high that SPI had to expand the floor space from about 3,500 square feet to more than 5,000 square feet (330-470 m2), says Brad Williams, director of trade shows sales and marketing for SPI. There’s been “some immediate good feedback once [exhibitors] buy the booths,” Williams notes, “and the feedback we’ve had from the industry in general has been good; they feel it’s indeed something that needs to be talked about.”
In building this “world within a world” exhibit space, Williams says, “We thought 3-D printing was important. It can be disruptive, and that’s part of the conversation: How disruptive will 3-D printing be, or will it be disruptive?”
Working Parts
Additive manufacturing is making strides in producing lighter working parts for automotive and aviation applications to save fuel consumption and costs.
Joining Arburg as co-sponsor of NPE3D is PolyOne, the material sponsor. NPE3D “enables attendees to explore emerging 3-D printing trends and technologies behind working parts produced directly from digital files, including three-dimensional prototypes, mold components, and even finished parts,” explains Thomas Hughes, Open Innovation program director. “We chose to sponsor this event to support our customers in their quest to understand the technology and the ways it can be leveraged in their operations.”
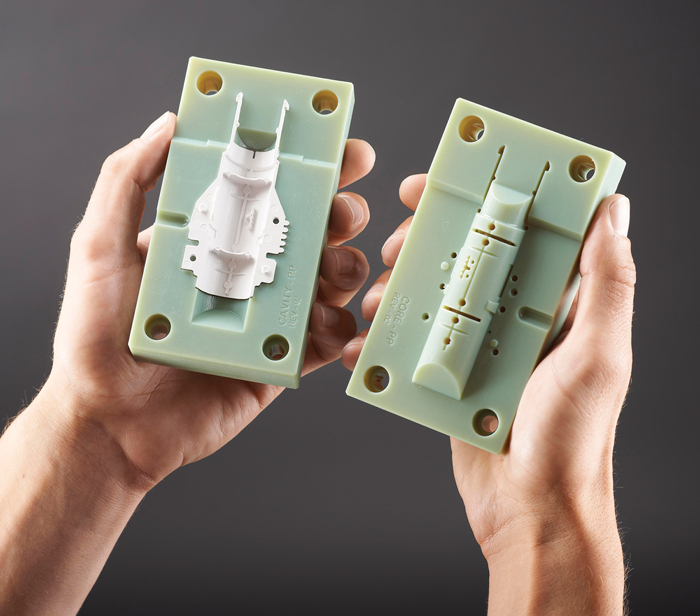
Injection mold components, produced with a multi-material 3-D printing capability, will be exhibited at NPE2015 by Stratasys (photo courtesy of Stratasys).
Stratasys will demonstrate a wealth of expertise in high-value industries across the board. “Folks are very familiar with 3-D printing,” says Bruce Bradshaw, vice president of marketing, North America. “It’s in the limelight all the time.” What’s changing, he says—and what the company will emphasize at NPE3D—“is how 3-D printing is used for manufacturing.” The company aims to answer the questions most on the minds of industry:
- “How can I employ 3-D printing and change my manufacturing floor?”
- “How can I augment my injection molding?”
- “How can I do tool verification [utilizing 3-D printers] before I spend $200,000 for a tool?”
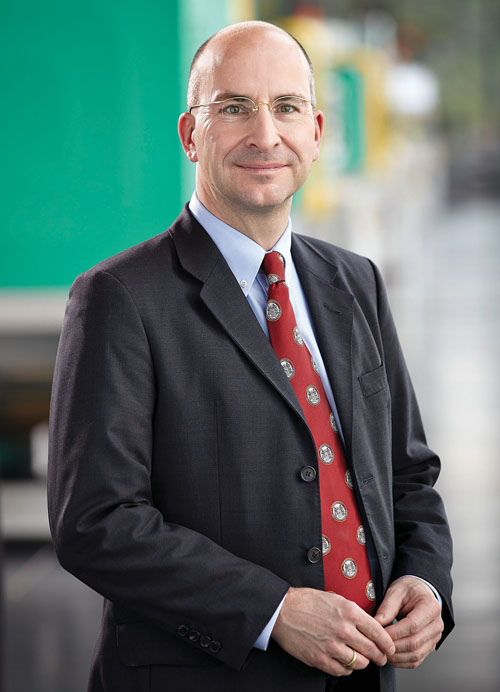
Heinz Gaub, managing director of Technology & Engineering, Arburg, and ANTEC® Orlando 2015 plenary speaker.
Stratasys is a hot commodity when it comes to general trade shows seeking its presence. “NPE for us is a much, much better show” than many of the more hobbyist-oriented events, explains Bradshaw, “because the people walking [the NPE] show floor are industrial buyers—people who are looking to use professional-level 3-D printers to advance their product development” on the manufacturing, R&D, or design sides.
Freeforming Concepts
Arburg, which will display its equipment outside the NPE3D pavilion in the main NPE space, began working on its Freeformer machine in 2004, when the company “began to think about producing plastic parts without molds,” Gaub explains.
“The idea of ‘free-flowing plastic droplets’ was followed by initial designs and basic trials which resulted in the patenting of the Arburg Plastic Freeforming process. We began collaborating in the area of droplet formation with a well-known university in 2007, and the first components were produced three years later. The Freeformer has been production-ready since 2014.
“Our initial target group comprises plastics processors who want to increase their flexibility and extend their portfolio to include additive manufacturing.” The system allows the efficient production of fully functional parts
“individually or as multiple-variant small-volume batches,” adds Gaub. “The Freeformer is also of interest to prototype engineers, designers, product developers, and rapid manufacturing service providers who want to produce prototypes and individual functional samples.”
Much confusion abounds about the variety of 3-D printing machines, as mainstream media tout more consumer-oriented uses with relatively inexpensive home-use machines that turn out low-value pieces. “The Freeformer cannot be compared with simple 3-D printers,” Gaub explains. “It is designed for industrial production; the technology is designed for continuous use and precision. Products made using 3-D CAD data in an additive manufacturing process are fully functional, quality parts.”
What makes the Freeformer unique, he says, “is the new way in which the material is prepared. As in injection molding, conventional plastic granulate is first plasticized by means of a screw, after which is it applied in layers to a moving component carrier in the form of tiny droplets of plastic. “As the process uses melted plastic, there is no problem with dust or emissions—unlike most conventional additive manufacturing processes.”
Also, he notes there are no “hidden costs” for expensive special materials. “[S]everal materials can be processed, for example, to produce parts in two colors, hard-soft combinations, or complex geometries with the help of water-soluble support structures…. In addition, it is possible to implement geometries that would be impossible to demold in a conventional injection molding process,” Gaub concludes.
“Horizontal Appeal”
At PolyOne, Hughes says, “we see manufacturers using selective laser sintering [SLS], fused deposition modeling [FDM], and stereolithography in niche applications with relatively low production volumes and high product value, such as aerospace interiors, automotive parts, medical devices, customized consumer products, and sporting goods.
“The next horizon… is still in question, but many see higher production volumes and larger build envelopes as real possibilities.” Hughes says PolyOne is focusing on “high-temperature aerospace material development for 3-D processes. We are collaborating with academic, government, and manufacturing partners to develop 3-D printing materials for fully functional production parts in aerospace and automotive applications.”
At Stratasys, the company likes to say that 3-D printing has “horizontal appeal; it doesn’t really matter what industry you’re in,” Bradshaw says. Automotive and aerospace parties are “huge users” of the company’s equipment, he adds, as are makers of consumer electronics and consumer goods. “But the medical industry has a lot of cachet in terms of its appeal for media and videos and things along those lines.”
While Europe is often cited as demonstrating leadership in additive manufacturing, particularly in automotive and dentistry, the USA represents about 55% of the company’s 3-D printing business, Bradshaw notes, while “Asia Pacific is growing by leaps and bounds.… The industry is growing so rapidly that the need is [evident] across all regions.”
In terms of materials—as in plastics vs. metals—the 3-D printing of metals is “stealing the limelight because it’s cool [and] there are some interesting applications for it,” he observes. “But if you look at the installed base of metal printers in the world, and specifically the USA, it pales in comparison to the number of 3-D printers that are doing plastics. The biggest need and the most understood area is in plastics.”
Bradshaw says about 25% of R&D investment for Stratasys is devoted to developing new materials. “It’s one thing to have a printer that spits something out, but it’s another thing to have a printer that spits out materials that matter to the people who are utilizing 3-D printers.”
Joining Stratasys at NPE will be sister company RedEye, a service bureau that has grown larger with the recent acquisition of Solid Concepts and Harvest Technologies. “They have technologies that Stratasys doesn’t have,” says Bradshaw. “We will be highlighting the capabilities of the service bureaus in our booth, and they will be highlighting the equipment in their booth.”
Covering Many Bases in the USA
In assessing the range of exhibitors at NPE3D, Williams notes that SPI has struck a balance in representing materials and machine companies, while also stressing that some of the firms aren’t widely known. This will let attendees “see some of the newer companies in the market.”
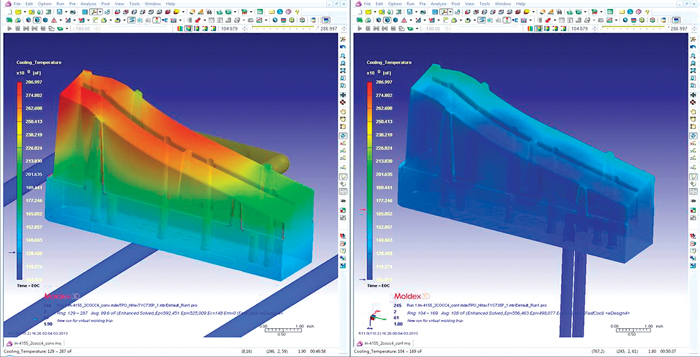
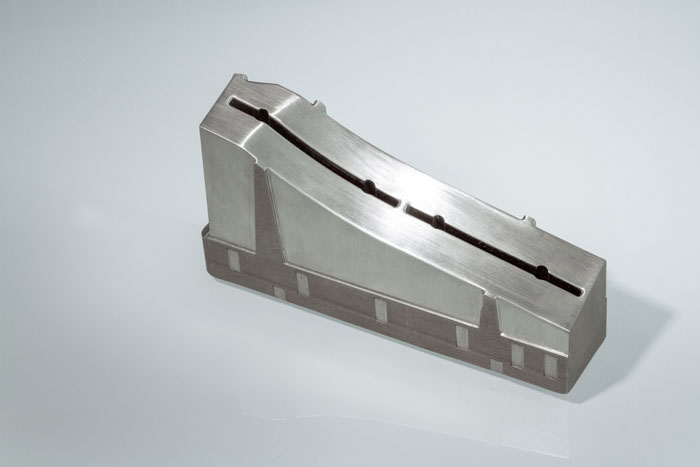
Differences in heating/cooling in a traditional vs. conformal cooling insert (above), as shown in this simulation image of an actual 3-D printed insert (below) from Linear Mold & Engineering (images courtesy of Linear).
Advanced RP of Suwanee, Georgia, is primarily a reseller of Stratasys rapid-prototyping technology, says Michael Brenholt, training and applications specialist. “We’re bringing Stratasys equipment, technology, and parts to showcase at NPE. We have a presence in Florida, and we want to make sure we can interact with our customers who are going to be in that area.”
Advanced RP deals with clients from hydraulic companies to automotive and aerospace. Recently, “we’ve been doing a lot with medical companies, whether it’s manufacturing or even with hospitals,” says Brenholt. “We’re working with a hospital right now to install a system for very special surgeries they’re working on.”
Other clients are using the technology “for a lot of jigs, fixtures, and tooling—a huge application I think has been overlooked in the past. People are starting to see past just tapping into 3-D printers for the purpose of prototyping a part.”
Linear Mold & Engineering of Livonia, Michigan, will “display our unique 3-D metal printing capabilities and continue to spread the word on how Linear is North America’s largest privately owned provider of 3-D metal-printing services, as well as a complete mold shop,” says marketing and sales coordinator Kristen Eisiminger.
“We will be bringing conformal-cooled inserts to show how we have developed a niche of using 3-D metal printing to build conformal cooling lines to complement our mold manufacturing business. Conformal water lines address the limitations of traditional machining. The benefits of using 3-D metal printing and conformal cooling include greater flexibility in creating water lines, better access to hard-to-reach areas, and significant cycle-time reductions. We will also bring a variety of 3-D metal-printed end-use parts used in industries such as aerospace, medical, automotive, and many more.”
Forecast 3D of Carlsbad, California, is also bringing several cool items to exhibit. “With NPE being such a large show with broad appeal to all things manufacturing and plastics—and with more and more attention on the 3-D printing space, including this year’s NPE3D—we are happy to be exhibiting at NPE for the first time,” says Donovan Weber, COO and co-founder.
At Forecast 3D’s booth, “We’ll have a 3-D printed electric bike, a 3-D printed ukulele, and many more 3-D printed parts that were built in a variety of technologies and materials,” adds Kimi Canete, director of marketing.
Founded in 1994 by Weber with his brother, Corey, Forecast 3D also brings a wealth of knowledge from the full spectrum of 3-D printing, rapid machining and tooling. “The entry of large-format FDM printers, specifically the BAAM [Big Area Additive Manufacturing] printer by Cincinnati [Inc.], as well as others, are an exciting new future potential for end-use production,” Weber explains.
“The attention is certainly on the manufacturing community of 3-D printing equipment, but it’s the growing focus on the materials R&D that further moves us from the prototyping market into end-use production. We are seeing the engineering community continuing to design for additive manufacturing and leverage these technologies.”
NPE in 3-D
Previous Article Next Article
By Geoff Giordano
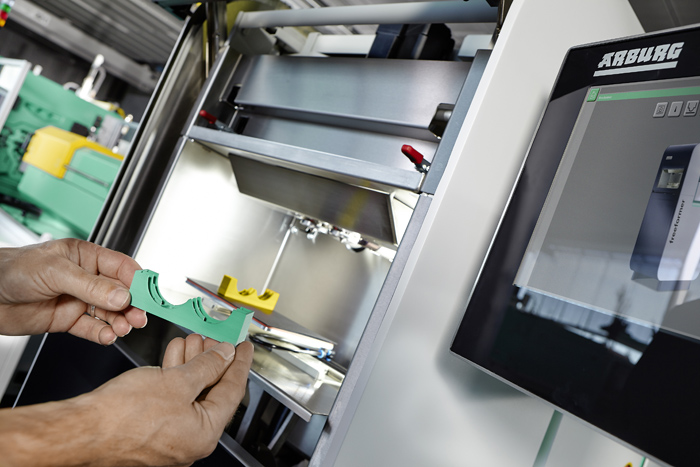
Arburg’s Freeformer 3-D-prints functional parts in thermoplastic resins. Because it works with molten plastic, it produces no dust or emissions, and it can be used to mass-produce items with customization, like three-dimensional lettering. (Photo courtesy of Arburg.)
When manufacturing equipment maker Arburg decided to become a sponsor of the first-ever NPE3D pavilion at NPE2015 in Orlando in March, it was an obvious win-win situation.
“We celebrated the premiere of our Freeformer at K [Show] 2013,” says Heinz Gaub, managing director of Technology & Engineering for Arburg (and an ANTEC® Orlando 2015 plenary speaker). “In 2014, the first development customers in Germany received delivery of this system for industrial additive manufacturing. The next phase in the region-by-region introduction will see the product launch in the European and overseas markets in spring 2015.
“We deliberately decided to schedule the Freeformer’s sales launch in America to coincide with the NPE show. NPE3D offers us the perfect platform for making contact with plastics processors from outside the injection molding sector in the U.S.”
With the 3-D printing revolution in full swing, NPE2015 has created a dedicated exhibit area featuring nearly 20 companies representing many facets of additive manufacturing. In addition, SPI has scheduled six 3-D printing presentations on Tuesday, March 24, during its Business of Plastics Conference.
Demand for the NPE3D pavilion was so high that SPI had to expand the floor space from about 3,500 square feet to more than 5,000 square feet (330-470 m2), says Brad Williams, director of trade shows sales and marketing for SPI. There’s been “some immediate good feedback once [exhibitors] buy the booths,” Williams notes, “and the feedback we’ve had from the industry in general has been good; they feel it’s indeed something that needs to be talked about.”
In building this “world within a world” exhibit space, Williams says, “We thought 3-D printing was important. It can be disruptive, and that’s part of the conversation: How disruptive will 3-D printing be, or will it be disruptive?”
Working Parts
Additive manufacturing is making strides in producing lighter working parts for automotive and aviation applications to save fuel consumption and costs.
Joining Arburg as co-sponsor of NPE3D is PolyOne, the material sponsor. NPE3D “enables attendees to explore emerging 3-D printing trends and technologies behind working parts produced directly from digital files, including three-dimensional prototypes, mold components, and even finished parts,” explains Thomas Hughes, Open Innovation program director. “We chose to sponsor this event to support our customers in their quest to understand the technology and the ways it can be leveraged in their operations.”
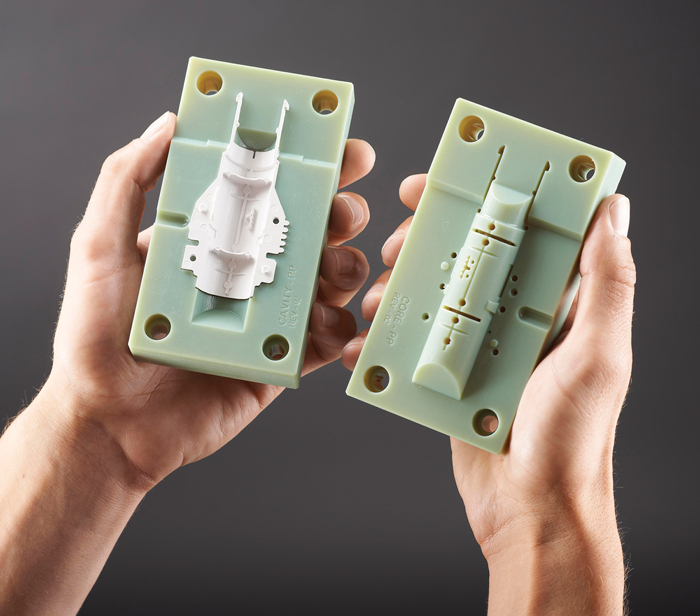
Injection mold components, produced with a multi-material 3-D printing capability, will be exhibited at NPE2015 by Stratasys (photo courtesy of Stratasys).
Stratasys will demonstrate a wealth of expertise in high-value industries across the board. “Folks are very familiar with 3-D printing,” says Bruce Bradshaw, vice president of marketing, North America. “It’s in the limelight all the time.” What’s changing, he says—and what the company will emphasize at NPE3D—“is how 3-D printing is used for manufacturing.” The company aims to answer the questions most on the minds of industry:
- “How can I employ 3-D printing and change my manufacturing floor?”
- “How can I augment my injection molding?”
- “How can I do tool verification [utilizing 3-D printers] before I spend $200,000 for a tool?”
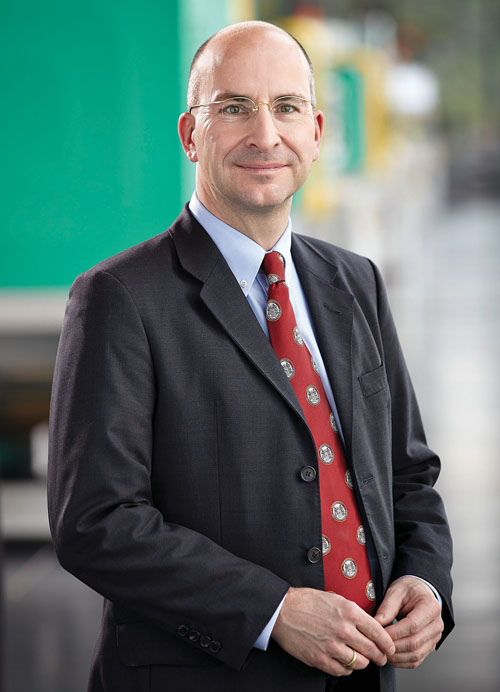
Heinz Gaub, managing director of Technology & Engineering, Arburg, and ANTEC® Orlando 2015 plenary speaker.
Stratasys is a hot commodity when it comes to general trade shows seeking its presence. “NPE for us is a much, much better show” than many of the more hobbyist-oriented events, explains Bradshaw, “because the people walking [the NPE] show floor are industrial buyers—people who are looking to use professional-level 3-D printers to advance their product development” on the manufacturing, R&D, or design sides.
Freeforming Concepts
Arburg, which will display its equipment outside the NPE3D pavilion in the main NPE space, began working on its Freeformer machine in 2004, when the company “began to think about producing plastic parts without molds,” Gaub explains.
“The idea of ‘free-flowing plastic droplets’ was followed by initial designs and basic trials which resulted in the patenting of the Arburg Plastic Freeforming process. We began collaborating in the area of droplet formation with a well-known university in 2007, and the first components were produced three years later. The Freeformer has been production-ready since 2014.
“Our initial target group comprises plastics processors who want to increase their flexibility and extend their portfolio to include additive manufacturing.” The system allows the efficient production of fully functional parts
“individually or as multiple-variant small-volume batches,” adds Gaub. “The Freeformer is also of interest to prototype engineers, designers, product developers, and rapid manufacturing service providers who want to produce prototypes and individual functional samples.”
Much confusion abounds about the variety of 3-D printing machines, as mainstream media tout more consumer-oriented uses with relatively inexpensive home-use machines that turn out low-value pieces. “The Freeformer cannot be compared with simple 3-D printers,” Gaub explains. “It is designed for industrial production; the technology is designed for continuous use and precision. Products made using 3-D CAD data in an additive manufacturing process are fully functional, quality parts.”
What makes the Freeformer unique, he says, “is the new way in which the material is prepared. As in injection molding, conventional plastic granulate is first plasticized by means of a screw, after which is it applied in layers to a moving component carrier in the form of tiny droplets of plastic. “As the process uses melted plastic, there is no problem with dust or emissions—unlike most conventional additive manufacturing processes.”
Also, he notes there are no “hidden costs” for expensive special materials. “[S]everal materials can be processed, for example, to produce parts in two colors, hard-soft combinations, or complex geometries with the help of water-soluble support structures…. In addition, it is possible to implement geometries that would be impossible to demold in a conventional injection molding process,” Gaub concludes.
“Horizontal Appeal”
At PolyOne, Hughes says, “we see manufacturers using selective laser sintering [SLS], fused deposition modeling [FDM], and stereolithography in niche applications with relatively low production volumes and high product value, such as aerospace interiors, automotive parts, medical devices, customized consumer products, and sporting goods.
“The next horizon… is still in question, but many see higher production volumes and larger build envelopes as real possibilities.” Hughes says PolyOne is focusing on “high-temperature aerospace material development for 3-D processes. We are collaborating with academic, government, and manufacturing partners to develop 3-D printing materials for fully functional production parts in aerospace and automotive applications.”
At Stratasys, the company likes to say that 3-D printing has “horizontal appeal; it doesn’t really matter what industry you’re in,” Bradshaw says. Automotive and aerospace parties are “huge users” of the company’s equipment, he adds, as are makers of consumer electronics and consumer goods. “But the medical industry has a lot of cachet in terms of its appeal for media and videos and things along those lines.”
While Europe is often cited as demonstrating leadership in additive manufacturing, particularly in automotive and dentistry, the USA represents about 55% of the company’s 3-D printing business, Bradshaw notes, while “Asia Pacific is growing by leaps and bounds.… The industry is growing so rapidly that the need is [evident] across all regions.”
In terms of materials—as in plastics vs. metals—the 3-D printing of metals is “stealing the limelight because it’s cool [and] there are some interesting applications for it,” he observes. “But if you look at the installed base of metal printers in the world, and specifically the USA, it pales in comparison to the number of 3-D printers that are doing plastics. The biggest need and the most understood area is in plastics.”
Bradshaw says about 25% of R&D investment for Stratasys is devoted to developing new materials. “It’s one thing to have a printer that spits something out, but it’s another thing to have a printer that spits out materials that matter to the people who are utilizing 3-D printers.”
Joining Stratasys at NPE will be sister company RedEye, a service bureau that has grown larger with the recent acquisition of Solid Concepts and Harvest Technologies. “They have technologies that Stratasys doesn’t have,” says Bradshaw. “We will be highlighting the capabilities of the service bureaus in our booth, and they will be highlighting the equipment in their booth.”
Covering Many Bases in the USA
In assessing the range of exhibitors at NPE3D, Williams notes that SPI has struck a balance in representing materials and machine companies, while also stressing that some of the firms aren’t widely known. This will let attendees “see some of the newer companies in the market.”
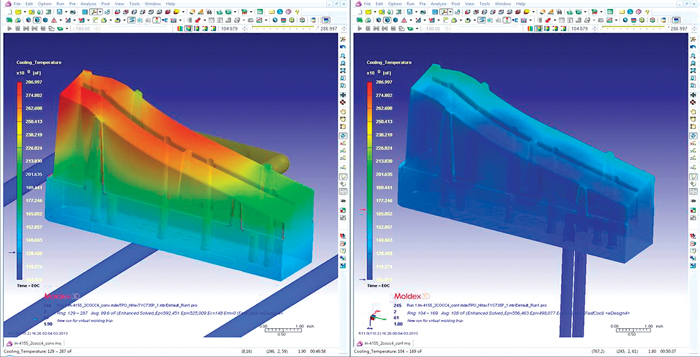
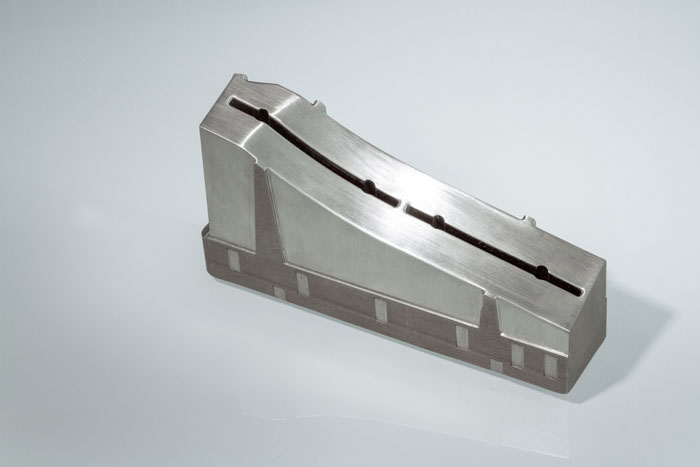
Differences in heating/cooling in a traditional vs. conformal cooling insert (above), as shown in this simulation image of an actual 3-D printed insert (below) from Linear Mold & Engineering (images courtesy of Linear).
Advanced RP of Suwanee, Georgia, is primarily a reseller of Stratasys rapid-prototyping technology, says Michael Brenholt, training and applications specialist. “We’re bringing Stratasys equipment, technology, and parts to showcase at NPE. We have a presence in Florida, and we want to make sure we can interact with our customers who are going to be in that area.”
Advanced RP deals with clients from hydraulic companies to automotive and aerospace. Recently, “we’ve been doing a lot with medical companies, whether it’s manufacturing or even with hospitals,” says Brenholt. “We’re working with a hospital right now to install a system for very special surgeries they’re working on.”
Other clients are using the technology “for a lot of jigs, fixtures, and tooling—a huge application I think has been overlooked in the past. People are starting to see past just tapping into 3-D printers for the purpose of prototyping a part.”
Linear Mold & Engineering of Livonia, Michigan, will “display our unique 3-D metal printing capabilities and continue to spread the word on how Linear is North America’s largest privately owned provider of 3-D metal-printing services, as well as a complete mold shop,” says marketing and sales coordinator Kristen Eisiminger.
“We will be bringing conformal-cooled inserts to show how we have developed a niche of using 3-D metal printing to build conformal cooling lines to complement our mold manufacturing business. Conformal water lines address the limitations of traditional machining. The benefits of using 3-D metal printing and conformal cooling include greater flexibility in creating water lines, better access to hard-to-reach areas, and significant cycle-time reductions. We will also bring a variety of 3-D metal-printed end-use parts used in industries such as aerospace, medical, automotive, and many more.”
Forecast 3D of Carlsbad, California, is also bringing several cool items to exhibit. “With NPE being such a large show with broad appeal to all things manufacturing and plastics—and with more and more attention on the 3-D printing space, including this year’s NPE3D—we are happy to be exhibiting at NPE for the first time,” says Donovan Weber, COO and co-founder.
At Forecast 3D’s booth, “We’ll have a 3-D printed electric bike, a 3-D printed ukulele, and many more 3-D printed parts that were built in a variety of technologies and materials,” adds Kimi Canete, director of marketing.
Founded in 1994 by Weber with his brother, Corey, Forecast 3D also brings a wealth of knowledge from the full spectrum of 3-D printing, rapid machining and tooling. “The entry of large-format FDM printers, specifically the BAAM [Big Area Additive Manufacturing] printer by Cincinnati [Inc.], as well as others, are an exciting new future potential for end-use production,” Weber explains.
“The attention is certainly on the manufacturing community of 3-D printing equipment, but it’s the growing focus on the materials R&D that further moves us from the prototyping market into end-use production. We are seeing the engineering community continuing to design for additive manufacturing and leverage these technologies.”
NPE in 3-D
Previous Article Next Article
By Geoff Giordano
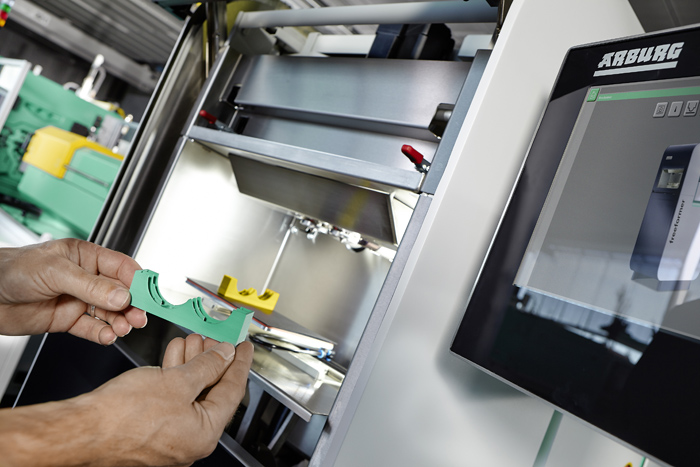
Arburg’s Freeformer 3-D-prints functional parts in thermoplastic resins. Because it works with molten plastic, it produces no dust or emissions, and it can be used to mass-produce items with customization, like three-dimensional lettering. (Photo courtesy of Arburg.)
When manufacturing equipment maker Arburg decided to become a sponsor of the first-ever NPE3D pavilion at NPE2015 in Orlando in March, it was an obvious win-win situation.
“We celebrated the premiere of our Freeformer at K [Show] 2013,” says Heinz Gaub, managing director of Technology & Engineering for Arburg (and an ANTEC® Orlando 2015 plenary speaker). “In 2014, the first development customers in Germany received delivery of this system for industrial additive manufacturing. The next phase in the region-by-region introduction will see the product launch in the European and overseas markets in spring 2015.
“We deliberately decided to schedule the Freeformer’s sales launch in America to coincide with the NPE show. NPE3D offers us the perfect platform for making contact with plastics processors from outside the injection molding sector in the U.S.”
With the 3-D printing revolution in full swing, NPE2015 has created a dedicated exhibit area featuring nearly 20 companies representing many facets of additive manufacturing. In addition, SPI has scheduled six 3-D printing presentations on Tuesday, March 24, during its Business of Plastics Conference.
Demand for the NPE3D pavilion was so high that SPI had to expand the floor space from about 3,500 square feet to more than 5,000 square feet (330-470 m2), says Brad Williams, director of trade shows sales and marketing for SPI. There’s been “some immediate good feedback once [exhibitors] buy the booths,” Williams notes, “and the feedback we’ve had from the industry in general has been good; they feel it’s indeed something that needs to be talked about.”
In building this “world within a world” exhibit space, Williams says, “We thought 3-D printing was important. It can be disruptive, and that’s part of the conversation: How disruptive will 3-D printing be, or will it be disruptive?”
Working Parts
Additive manufacturing is making strides in producing lighter working parts for automotive and aviation applications to save fuel consumption and costs.
Joining Arburg as co-sponsor of NPE3D is PolyOne, the material sponsor. NPE3D “enables attendees to explore emerging 3-D printing trends and technologies behind working parts produced directly from digital files, including three-dimensional prototypes, mold components, and even finished parts,” explains Thomas Hughes, Open Innovation program director. “We chose to sponsor this event to support our customers in their quest to understand the technology and the ways it can be leveraged in their operations.”
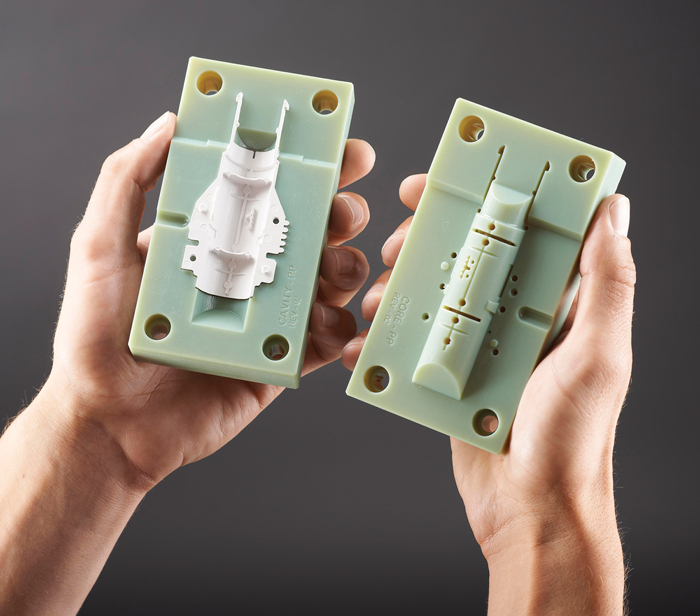
Injection mold components, produced with a multi-material 3-D printing capability, will be exhibited at NPE2015 by Stratasys (photo courtesy of Stratasys).
Stratasys will demonstrate a wealth of expertise in high-value industries across the board. “Folks are very familiar with 3-D printing,” says Bruce Bradshaw, vice president of marketing, North America. “It’s in the limelight all the time.” What’s changing, he says—and what the company will emphasize at NPE3D—“is how 3-D printing is used for manufacturing.” The company aims to answer the questions most on the minds of industry:
- “How can I employ 3-D printing and change my manufacturing floor?”
- “How can I augment my injection molding?”
- “How can I do tool verification [utilizing 3-D printers] before I spend $200,000 for a tool?”
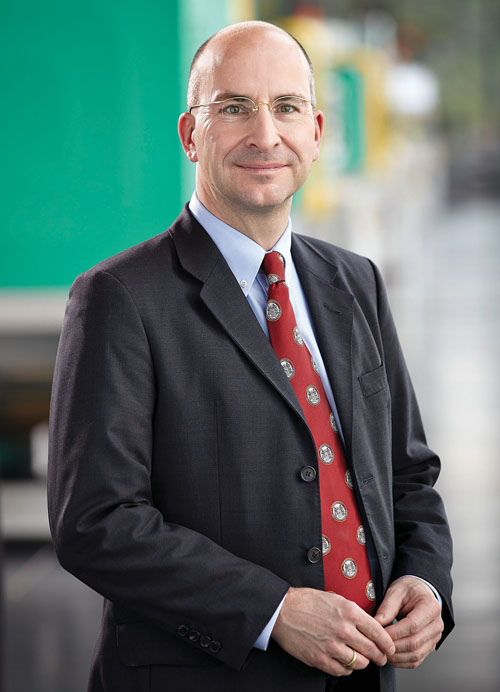
Heinz Gaub, managing director of Technology & Engineering, Arburg, and ANTEC® Orlando 2015 plenary speaker.
Stratasys is a hot commodity when it comes to general trade shows seeking its presence. “NPE for us is a much, much better show” than many of the more hobbyist-oriented events, explains Bradshaw, “because the people walking [the NPE] show floor are industrial buyers—people who are looking to use professional-level 3-D printers to advance their product development” on the manufacturing, R&D, or design sides.
Freeforming Concepts
Arburg, which will display its equipment outside the NPE3D pavilion in the main NPE space, began working on its Freeformer machine in 2004, when the company “began to think about producing plastic parts without molds,” Gaub explains.
“The idea of ‘free-flowing plastic droplets’ was followed by initial designs and basic trials which resulted in the patenting of the Arburg Plastic Freeforming process. We began collaborating in the area of droplet formation with a well-known university in 2007, and the first components were produced three years later. The Freeformer has been production-ready since 2014.
“Our initial target group comprises plastics processors who want to increase their flexibility and extend their portfolio to include additive manufacturing.” The system allows the efficient production of fully functional parts
“individually or as multiple-variant small-volume batches,” adds Gaub. “The Freeformer is also of interest to prototype engineers, designers, product developers, and rapid manufacturing service providers who want to produce prototypes and individual functional samples.”
Much confusion abounds about the variety of 3-D printing machines, as mainstream media tout more consumer-oriented uses with relatively inexpensive home-use machines that turn out low-value pieces. “The Freeformer cannot be compared with simple 3-D printers,” Gaub explains. “It is designed for industrial production; the technology is designed for continuous use and precision. Products made using 3-D CAD data in an additive manufacturing process are fully functional, quality parts.”
What makes the Freeformer unique, he says, “is the new way in which the material is prepared. As in injection molding, conventional plastic granulate is first plasticized by means of a screw, after which is it applied in layers to a moving component carrier in the form of tiny droplets of plastic. “As the process uses melted plastic, there is no problem with dust or emissions—unlike most conventional additive manufacturing processes.”
Also, he notes there are no “hidden costs” for expensive special materials. “[S]everal materials can be processed, for example, to produce parts in two colors, hard-soft combinations, or complex geometries with the help of water-soluble support structures…. In addition, it is possible to implement geometries that would be impossible to demold in a conventional injection molding process,” Gaub concludes.
“Horizontal Appeal”
At PolyOne, Hughes says, “we see manufacturers using selective laser sintering [SLS], fused deposition modeling [FDM], and stereolithography in niche applications with relatively low production volumes and high product value, such as aerospace interiors, automotive parts, medical devices, customized consumer products, and sporting goods.
“The next horizon… is still in question, but many see higher production volumes and larger build envelopes as real possibilities.” Hughes says PolyOne is focusing on “high-temperature aerospace material development for 3-D processes. We are collaborating with academic, government, and manufacturing partners to develop 3-D printing materials for fully functional production parts in aerospace and automotive applications.”
At Stratasys, the company likes to say that 3-D printing has “horizontal appeal; it doesn’t really matter what industry you’re in,” Bradshaw says. Automotive and aerospace parties are “huge users” of the company’s equipment, he adds, as are makers of consumer electronics and consumer goods. “But the medical industry has a lot of cachet in terms of its appeal for media and videos and things along those lines.”
While Europe is often cited as demonstrating leadership in additive manufacturing, particularly in automotive and dentistry, the USA represents about 55% of the company’s 3-D printing business, Bradshaw notes, while “Asia Pacific is growing by leaps and bounds.… The industry is growing so rapidly that the need is [evident] across all regions.”
In terms of materials—as in plastics vs. metals—the 3-D printing of metals is “stealing the limelight because it’s cool [and] there are some interesting applications for it,” he observes. “But if you look at the installed base of metal printers in the world, and specifically the USA, it pales in comparison to the number of 3-D printers that are doing plastics. The biggest need and the most understood area is in plastics.”
Bradshaw says about 25% of R&D investment for Stratasys is devoted to developing new materials. “It’s one thing to have a printer that spits something out, but it’s another thing to have a printer that spits out materials that matter to the people who are utilizing 3-D printers.”
Joining Stratasys at NPE will be sister company RedEye, a service bureau that has grown larger with the recent acquisition of Solid Concepts and Harvest Technologies. “They have technologies that Stratasys doesn’t have,” says Bradshaw. “We will be highlighting the capabilities of the service bureaus in our booth, and they will be highlighting the equipment in their booth.”
Covering Many Bases in the USA
In assessing the range of exhibitors at NPE3D, Williams notes that SPI has struck a balance in representing materials and machine companies, while also stressing that some of the firms aren’t widely known. This will let attendees “see some of the newer companies in the market.”
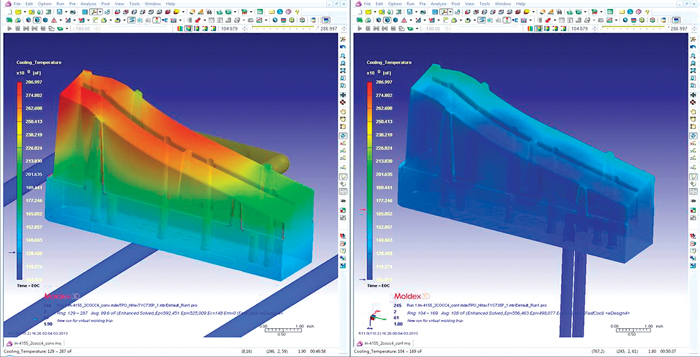
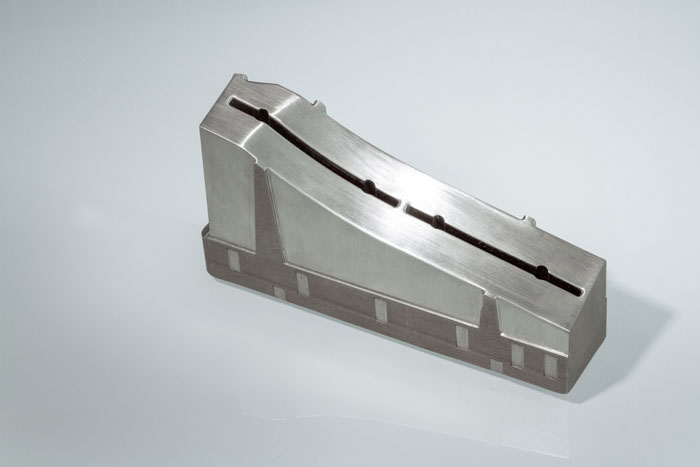
Differences in heating/cooling in a traditional vs. conformal cooling insert (above), as shown in this simulation image of an actual 3-D printed insert (below) from Linear Mold & Engineering (images courtesy of Linear).
Advanced RP of Suwanee, Georgia, is primarily a reseller of Stratasys rapid-prototyping technology, says Michael Brenholt, training and applications specialist. “We’re bringing Stratasys equipment, technology, and parts to showcase at NPE. We have a presence in Florida, and we want to make sure we can interact with our customers who are going to be in that area.”
Advanced RP deals with clients from hydraulic companies to automotive and aerospace. Recently, “we’ve been doing a lot with medical companies, whether it’s manufacturing or even with hospitals,” says Brenholt. “We’re working with a hospital right now to install a system for very special surgeries they’re working on.”
Other clients are using the technology “for a lot of jigs, fixtures, and tooling—a huge application I think has been overlooked in the past. People are starting to see past just tapping into 3-D printers for the purpose of prototyping a part.”
Linear Mold & Engineering of Livonia, Michigan, will “display our unique 3-D metal printing capabilities and continue to spread the word on how Linear is North America’s largest privately owned provider of 3-D metal-printing services, as well as a complete mold shop,” says marketing and sales coordinator Kristen Eisiminger.
“We will be bringing conformal-cooled inserts to show how we have developed a niche of using 3-D metal printing to build conformal cooling lines to complement our mold manufacturing business. Conformal water lines address the limitations of traditional machining. The benefits of using 3-D metal printing and conformal cooling include greater flexibility in creating water lines, better access to hard-to-reach areas, and significant cycle-time reductions. We will also bring a variety of 3-D metal-printed end-use parts used in industries such as aerospace, medical, automotive, and many more.”
Forecast 3D of Carlsbad, California, is also bringing several cool items to exhibit. “With NPE being such a large show with broad appeal to all things manufacturing and plastics—and with more and more attention on the 3-D printing space, including this year’s NPE3D—we are happy to be exhibiting at NPE for the first time,” says Donovan Weber, COO and co-founder.
At Forecast 3D’s booth, “We’ll have a 3-D printed electric bike, a 3-D printed ukulele, and many more 3-D printed parts that were built in a variety of technologies and materials,” adds Kimi Canete, director of marketing.
Founded in 1994 by Weber with his brother, Corey, Forecast 3D also brings a wealth of knowledge from the full spectrum of 3-D printing, rapid machining and tooling. “The entry of large-format FDM printers, specifically the BAAM [Big Area Additive Manufacturing] printer by Cincinnati [Inc.], as well as others, are an exciting new future potential for end-use production,” Weber explains.
“The attention is certainly on the manufacturing community of 3-D printing equipment, but it’s the growing focus on the materials R&D that further moves us from the prototyping market into end-use production. We are seeing the engineering community continuing to design for additive manufacturing and leverage these technologies.”